Maximum usable furnace space: Ø 1,500 mm/6,000 mm height
Maximum batch weight: 10.000 kg
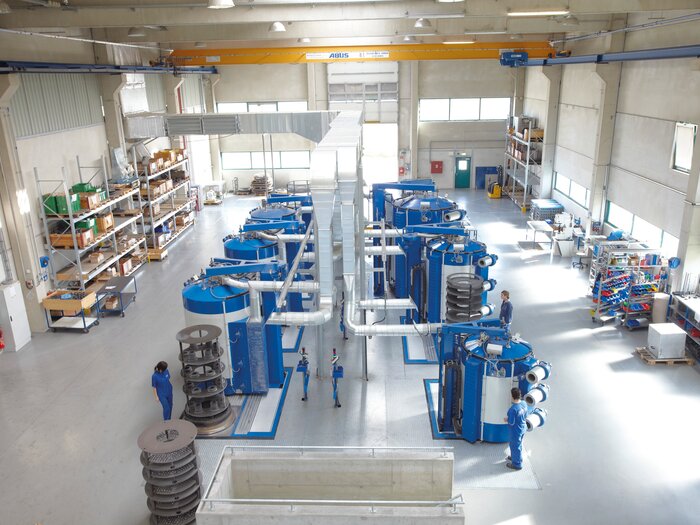
PLASOX® is a special treatment and describes our PLASNIT® processes with subsequent oxidation.
As a result of this targeted post-oxidation, an oxide layer is incorporated into the compound layer. In addition to improving the sliding properties, it causes an increase in corrosion resistance. The combination of plasma nitration and postoxidation can be carried out both in a single process and in two separate processes. The PLASOX® treatment turns the plasma nitrided parts dark gray to matte black.
We recommend PLASOX® for components that require a certain degree of corrosion inhibition and act as a friction partner for another hardened part.
Necessary information:
- Surface hardness
- Nitriding hardness depth
- Compound layer thickness/oxide layer thickness
- Definition of the area to be nitrided (as an indication on the construction drawing)
How can we support?
We are happy to advise you personally. Contact us and get detailed information about the treatment you want!
OUR PLASMA NITRIDING SYSTEM
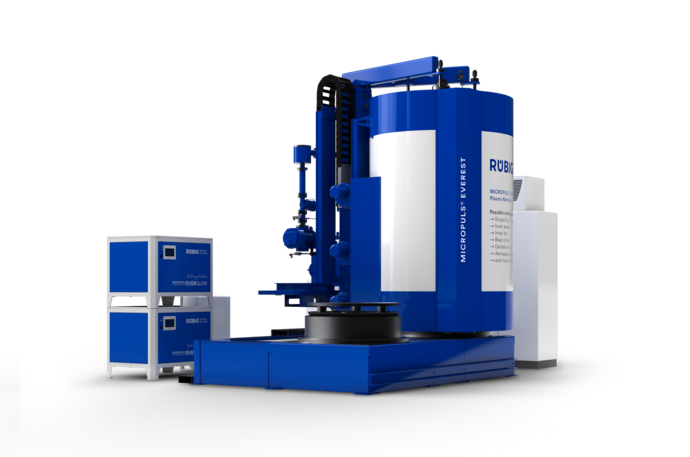
EVEREST
The plasma nitriding system MICROPULS® Everest offers our customers the cutting edge technology of nitriding. It is used in numerous industries, from automotive and contract heat treatment to aviation and wind energy.