Maximaler Ofennutzraum: 1.520 x 1.200 x 1.045 mm (L x B x H)
Maximales Chargengewicht: 2.300 kg
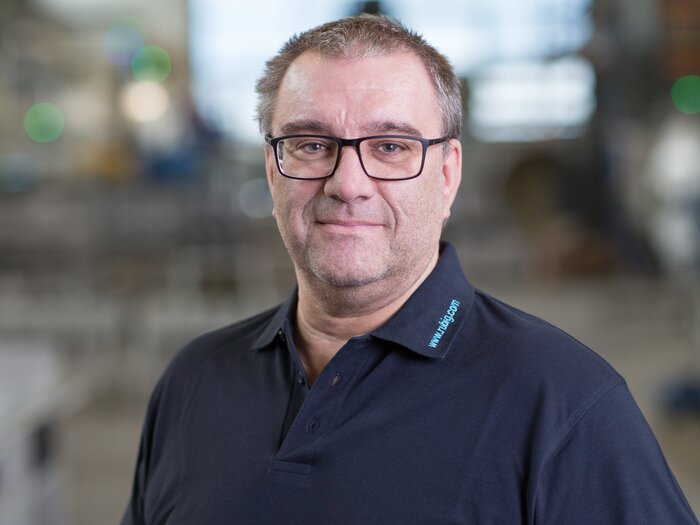
Das Einsatzhärten zählt zu den traditionellsten, thermochemischen Wärmebehandlungsverfahren. In enger Zusammenarbeit mit unseren Kunden können Bauteile auf maximale Maßhaltigkeit und engste Toleranzen optimiert werden.
Einsatzhärten ist nicht gleich Einsatzhärten. Unter R.CARB+® finden Sie die verschiedenen Einsatzhärteverfahren von RÜBIG. Enge Toleranzen und höchste Reproduzierbarkeit sind selbstverständlich. Auch Härte- und Maßstabilität zeichnen die R.CARB+® Verfahren von RÜBIG aus.
Werkstücke, die mit R.CARB+® behandelt werden, weisen eine erhöhte Dauerfestigkeit, einen verbesserten Verschleißwiderstand und eine Kombination aus hartem, verschleißbeständigem Rand und zähem Kern auf. Das Verfahren eignet sich besonders für Getriebeteile, Zahnräder, Wellen u. a.
R.Carb+® Verfahren im Überblick
Einsatzhärten
Einsatzhärten ist eine Kombination aus Aufkohlungs- und Härteprozess inklusive Anlassen. Dabei bildet sich ein aufgekohlter Randbereich mit einem Kohlenstoffgehalt von 0,6 - 0,8 %, der zum Kern hin kontinuierlich abnimmt. Nach dem Härteprozess entsteht ein Rand mit hoher Härte und einem weichen, zähen Kern. Für den Aufkohlungsprozess eignen sich Einsatzstähle mit Kohlenstoffgehalten unter 0,25 Massenprozent.
Vorteile:
- Erhöhte Dauerfestigkeit
- Gesteigerter Verschleißwiderstand
- Kombination aus hartem, verschleißbeständigen Rand und zähem Kern
Schutzgashärten
Bei diesem Durchhärteprozess werden die Bauteile (z. B. Werkzeuge) in einer reaktiven Atmosphäre vor einer negativen Beeinflussung der Randzone (z. B. Entkohlung) geschützt. Abgeschreckt wird beim Schutzgashärten in einem Ölbad, dadurch können auch unlegierte und niedriglegierte Stähle durchgehärtet werden. Durch weitere Behandlungen lassen sich Festigkeit, Zähigkeit, Verschleißbeständigkeit und andere Eigenschaften in einem weiten Bereich einstellen.
Schutzgashärten eignet für Vergütungsstähle (z. B. 1.7225), Kugellagerstahl (z.B. 1.3505) und Kohlenstoffstähle (z.B. C45)
Vorteile:
- Verbesserung der physikalischen Bauteileigenschaften
Carbonitrieren
Beim Carbonitrieren wird die Randzone eines Bauteils nicht nur mit Kohlenstoff, sondern zusätzlich mit Stickstoff angereichert. Dadurch wird die Härtbarkeit verbessert, was es ermöglicht, auch unlegierte Stähle (Baustähle) zu behandeln. Ähnlich wie beim Einsatzhärten entsteht ein harter und verschleißfester Randbereich mit hoher Festigkeit, während der Kern des Bauteils zäh bleibt.
Dieses Verfahren eignet sich besonders gut für bestimmte Bauteile wie Getriebeteile (Hohlräder, Stirnräder), Kurbelwellen und Antriebswellen. Eine spezielle Variante dieses Verfahrens ist das "HighCarb"-Verfahren, das durch eine besondere Prozessführung zu einer verbesserten Anlassbeständigkeit und Härtbarkeit führt. Dadurch werden die Bauteile besonders widerstandsfähig und langlebig.
Vorteile:
- Auch für unlegierte Stähle geeignet
High Carb
High Carb stellt eine Sondervariante des Carbonitrierens dar und führt zu einer verbesserten Härtbarkeit und
Anlassbeständigkeit.
Einsatzgebiet:
- Zum Einstellen der Festigkeits- und Zähigkeitseigenschaften für spezielle Bauteilgeometrien mit sehr hohen Anforderungen
- Erhöhung des Verschleißschutzes und der Dauerfestigkeitseigenschaften
- Erhöhung der Einsatztemperatur einsatzgehärteter Bauteile
Welche Branchen werden damit bedient:
- Werkzeugbau
- Automotive
- Aerospace
Aufkohlen
Beim Aufkohlen wird die äußere Schicht eines Stahls, üblicherweise Einsatzstähle, mit Kohlenstoff angereichert. Anschließend erfolgt eine langsame Abkühlung unter Schutzgasatmosphäre, um keine zusätzliche Härte zu erzeugen. Dadurch können die Bauteile bearbeitet werden, bevor der eigentliche Härteprozess stattfindet. Ein großer Vorteil dieses Verfahrens besteht darin, dass durch die Abdeckung kein zusätzliches Nacharbeiten erforderlich ist.
Werkstoffe, die für den Aufkohlungsprozess geeignet sind, weisen Kohlenstoffgehalte unter 0,25 Massenprozent auf und sind häufig Einsatzstähle.
Welche Branchen werden damit bedient:
- Werkzeug- und Maschinenbau
- Automotive
- Landmaschinen
- Aerospace
Vergüten
Beim Vergüten handelt es sich um eine besondere Kombination von Durchhärteverfahren (wie Vakuum- oder Schutzgashärten) und einem anschließenden Anlassen bei hoher Temperatur. Dieser Prozess wird auch oft als "QT" (quenched and tempered) abgekürzt.
Die Anlassbehandlung erfolgt bei hohen Temperaturen bis zu 700° C, um ein optimales Gleichgewicht aus Festigkeit und Zähigkeit zu erreichen. Daher ist das Vergüten besonders wichtig und sinnvoll für Bauteile, die dynamischen Belastungen, z.B. Wellen, ausgesetzt sind.
Geeignete Werkstoffe:
- Vergütungsstähle
Nitrierstähle
Werkzeugstähle (Kalt-, Warm- und Schnellarbeitsstähle)
Vorteile:
Gute Kombination von Zähigkeit und Festigkeit
Tiefkühlen
Das Tiefkühlen erfolgt normalerweise bei Temperaturen von bis zu -120° C und dauert einige Stunden. Eine zusätzliche Variante ist die sogenannte Cryotreatment oder Cryobehandlung. Bei diesem Verfahren wird die Temperatur sogar bis zu -196° C gesenkt und die Haltezeit geht weit über die übliche Durchwärmdauer hinaus.
Tiefkühlen ist immer dann sinnvoll oder notwendig, wenn Bauteile folgende Anforderungen erfüllen müssen:
Hohe Verschleißbeständigkeit:
Durch das Tiefkühlen erfolgt eine Umwandlung des Restaustenits in Martensit, was zu einer Erhöhung der Härte führt.
Maß- und Formstabilität:
Durch das Tiefkühlen wird ein stabiles und homogenes Gefüge erzielt, das während des Einsatzes kaum oder gar keine Veränderungen aufweist.
ANlassen
Beim Anlassen wird Stahl auf Niedrigtemperatur erwärmt, um Eigenschaften wie die Härte und Zähigkeit gezielt abzustimmen. In der Regel sollen durch das Anlassen Spannungen abgebaut werden, die durch vorheriges Härten des Werkstoffs aufgebaut wurden.
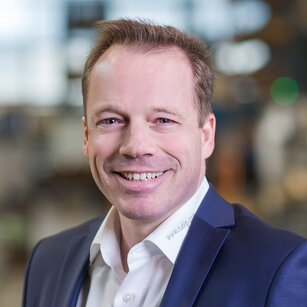
SIE HABEN NOCH OFFENE
FRAGEN?
RÜBIG Härtetechnik kombiniert modernste Technologie und fundierte Branchenkenntnis, um Ihre Stahlprodukte optimal zu veredeln.
DI David Unterberger
Vertriebsleiter Härtetechnik