PACVD Beschichtung:
DLcoat PLASTIT®
und DLC Xtended®
RÜBIG bietet im Bereich der kohlenstoffbasierten Beschichtungen zwei Hauptvarianten an, um unterschiedlichen Anforderungen gerecht zu werden: DLcoat PLASTIT® als Standard-DLC-Beschichtung bei niedriger Temperatur und DLC Xtended® als weiterentwickelte DLC-Schicht, die auch als Hartchrom-Alternative dient. Beide Verfahren basieren auf PACVD (Plasmaunterstützte CVD) und liefern harte, verschleißfeste Schichten, unterscheiden sich jedoch in Prozessführung und Anwendungsprofil.
Ein großer Vorteil der PACVD-Technologie bei RÜBIG ist die Flexibilität hinsichtlich Bauteilgeometrie. Im Gegensatz zu rein line-of-sight abhängigen Verfahren (z.B. PVD) können mit PACVD auch komplexe Formen und Innenkonturen gleichmäßig beschichtet werden.
Mit PACVD lassen sich selbst innenliegende Bohrungen ab ca. 5 mm Durchmesser mit DLC auskleiden. (Hierbei ist lediglich das Verhältnis von Bohrungsdurchmesser zu -länge zu beachten – sehr tiefe, dünne Kanäle sind begrenzt beschichtbar, da die Schichtdicke in der Tiefe abnimmt.)
RÜBIG hat Erfahrungen mit Innenbeschichtungen, bei denen die Abscheiderate innen sogar höher sein kann als außen. Dies eröffnet z.B. die Möglichkeit, Rohre, Zylinder oder Hohlwellen innen vor Verschleiß und Korrosion zu schützen, was mit vielen anderen Verfahren nicht umsetzbar ist.
Auch bei der Bauteilgröße ist RÜBIG gut aufgestellt: Die größte PACVD-Anlage fasst Teile bis zu Ø 1,4 m und 2 m Höhe. Damit können selbst große Walzen, Zylinderrohre oder Formen in einem Stück beschichtet werden. Für sehr kleine Bauteile steht hingegen die spezielle DLcoat-Anlage zur Verfügung (optimiert für Klein- und Präzisionsteile).
Beschichtbare Werkstoffe: DLC wird vorwiegend auf metallischen Werkstoffen eingesetzt. Besonders geeignet sind gehärtete Stähle, Werkzeugstähle sowie gängige Einsatz- und Nitrierstähle. Diese können ggf. direkt im DLC Xtended-Prozess nitriert werden. Edelstähle lassen sich ebenfalls beschichten; hier empfiehlt sich oft eine vorherige Plasmanitrierung zur Härtungssteigerung. Aluminium und andere NE-Metalle können mit DLC beschichtet werden, jedoch nur im reinen DLC-Prozess bei niedriger Temperatur (DLcoat), da sie die hohen Temperaturen einer Duplexbehandlung nicht vertragen würden. Wichtig ist, dass der Grundwerkstoff eine ausreichend hohe Anlassbeständigkeit mitbringt, wenn ein hochtemperatur Duplex-Prozess (450–500 °C) gewählt wird.
Oberflächenzustand und Vorbehandlung: Um optimale Beschichtungsergebnisse zu erzielen, sollte die Bauteiloberfläche metallisch sauber und möglichst glatt sein. RÜBIG empfiehlt z.B. Polieren oder Feinschleifen vor dem Beschichten, da die Rauigkeit durch die DLC-Schicht nur leicht reduziert wird bzw. die Schicht diese imitiert. Typischerweise steigt die Rauheit durch die Beschichtung minimal an. Des Weiteren müssen Oberflächen frei von Korrosion, Fetten und Rückständen sein. Als optionale Vorbehandlung kann RÜBIG ein Mikrostrahlen durchführen, um die Haftung zu fördern. Bei Bedarf wird auch ein Plasmanitrieren vor dem Beschichten durchgeführt (entweder als separater Schritt oder integriert im Duplex-Prozess). Ein großer Vorteil des PACVD-Verfahrens: Nach dem Beschichten sind keine Nacharbeiten erforderlich – die Schicht kommt fertig einsatzbereit aus der Anlage. Es entstehen keine Spritzer oder Droplets, die aufwändig entfernt werden müssten, und Maße bleiben innerhalb enger Toleranzen.
PACVD mit DL coat PLASTIT®
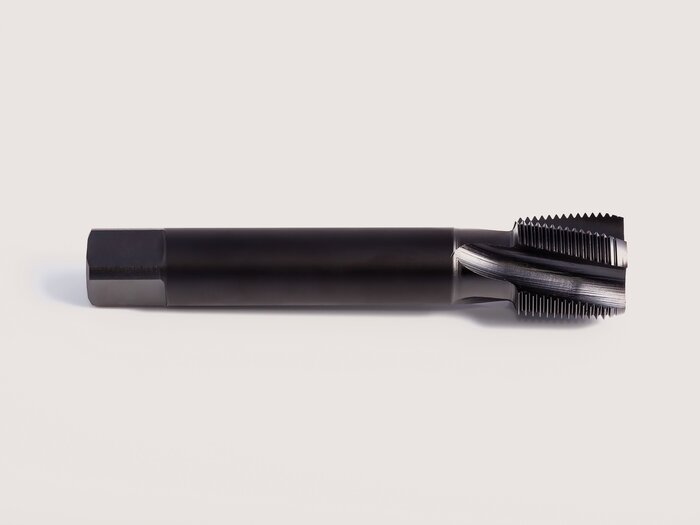
DLcoat PLASTIT® ist eine DLC-Beschichtung, die bereits bei ca. 150–200 °C aufgetragen wird. Sie wurde speziell für temperatursensible Bauteile und kleinere Komponenten entwickelt. Typische Eigenschaften dieser Schicht sind etwa 2 µm Schichtdicke bei ca. 2000 HV bis zu einer Härte von 3500 HV. Die Schichtfarbe ist anthrazit und die Oberfläche sehr glatt sowie nahezu frei von Partikeln oder Droplets, da das PACVD-Verfahren ein gleichmäßiges Schichtwachstum gewährleistet werden auch in der Kunststoffspritzgusstechnik verwendet oder für Auswerfer, Schieber und Bauteile eingesetzt, die aus produktionstechnischen Gründen keine Schmierung erhalten können.
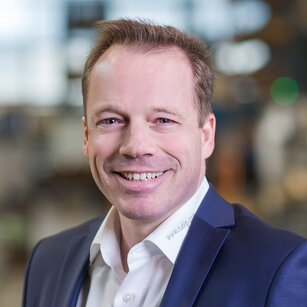
PACVD BeschichtungEN -
Wie kann ich helfen?
DLC bringt höchste Oberflächenleistung – und ich zeige Ihnen, wie Sie davon profitieren. Lassen Sie uns gemeinsam Ihre Möglichkeiten erörtern!
DI David Unterberger
Vertriebsleiter Härtetechnik
Wofür eignet sich DL Coat Plastit®
Vor allem für Bauteile, die einen soliden Grundverschleißschutz und Reibungsreduktion benötigen, jedoch keine extrem dicken Schichten erfordern. Beispiele sind Kunststoffspritzgussformen, Präzisionsbauteile, Ventile oder gleitende Maschinenelemente, die bei Fertigungstemperaturen unter 200 °C angelassen wurden. Auch Aluminiumteile können mit DLcoat beschichtet werden
Die Beschichtung verleiht diesen Komponenten eine deutlich erhöhte Lebensdauer, ohne maßliche Änderungen (DLC ~2 µm dünn) und ohne dass ein nachträgliches Polieren nötig wäre. DLcoat-Schichten sind zudem dekorativ einsetzbar, wenn etwa ein homogener anthrazitfarbener Look gewünscht ist
Hinweis: Aufgrund der kleineren Anlage für DLcoat können Bauteile bis maximal ca. 100 × 200 × 400 mm beschichtet werden. Für größere Teile oder höhere Schichtdicken kommt DLC Xtended® zum Einsatz.
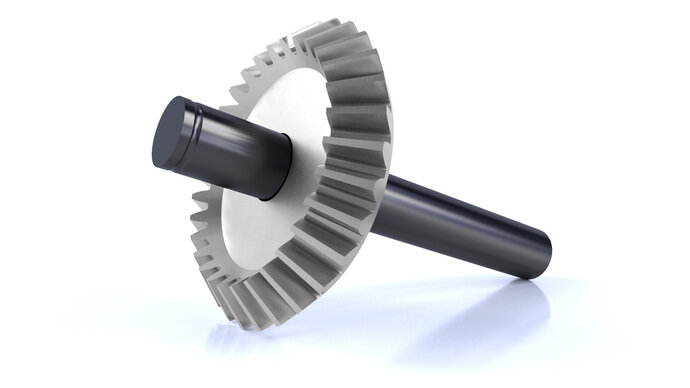
PACVD mit Dlc Xtended®
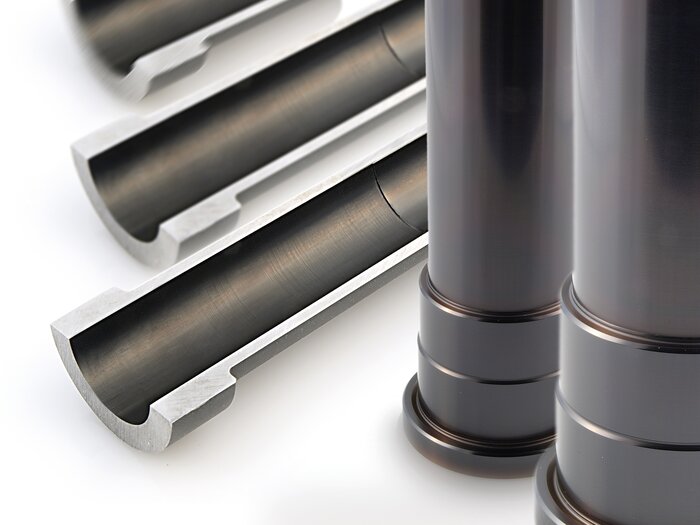
DLC Xtended® bezeichnet eine von RÜBIG entwickelte DLC-Beschichtung, die optional in Kombination mit einer Plasma-Nitrierung aufgebracht wird (Duplex-Prozess)
Dieses Verfahren erlaubt höhere Schichtdicken und verbessert die Anbindung der harten DLC-Schicht an den Grundwerkstoff durch eine graduelle Härteübergangszone (vermeidet den “Eggshell”-Effekt einer spröden Oberflächenschicht). Eine dünne Diffusionszone (~0,1–0,2 mm) im Stahl sorgt für Verankerung und zusätzliche Härte im Randbereich. Zudem wird bei RÜBIG immer eine Silizium-haltige Zwischenschicht (a-C:H:Si) an der Schicht/Material-Grenzfläche abgeschieden, welche die Haftung der DLC-Schicht exzellent sicherstellt.
DLC Xtended® wird typischerweise bei Temperaturen um 400–500 °C durchgeführt
Daher eignet sich dieses Verfahren vor allem für Stähle mit ausreichend hoher Anlassbeständigkeit (> 480 °C). Bei Bedarf kann DLC Xtended jedoch auch ohne vorheriges Nitrieren appliziert werden
– in diesem Fall bleibt die Prozesstemperatur niedriger (~450°C für die DLC-Abscheidung) und es wird ausschließlich die DLC-Schicht (mit Silizium-Bondlage) aufgebracht. RÜBIG kann so je nach Werkstoff und Anforderung flexibel entscheiden, ob ein Duplex-Verfahren (Nitrieren + DLC) oder nur DLC sinnvoll ist.
Durch die einzigartige Kombination von MICROPULS®-Plasmanitrieren und Hartstoffbeschichtung lassen sich Oberflächenhärten von 500 - 2500 HV erreichen.
Durch speziell entwickelte Verfahrensparameter können Durchgangsbohrungen mit einem Durchmesser im Längen-Verhältnis von 1:15 beschichtet werden (Mindestdurchmesser > 15 mm). Für diese Entwicklung erhielt RÜBIG in Frankreich den „Prix de l'Innovation“.
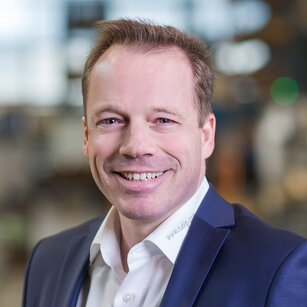
Wie kann ich helfen?
DLC bringt höchste Oberflächenleistung – und ich zeige Ihnen, wie Sie davon profitieren.
Lassen Sie uns gemeinsam Ihre Möglichkeiten erörtern!“
DI David Unterberger
Vertriebsleiter Härtetechnik
PACVD nach Beschichtungsart
"Harte" Schichten
Maximale Schichthärte von etwa 2500 HV für höchsten Verschleißschutz.
„Weiche“ Schichten
Etwas geringerer Härtebereich (Minimalhärten ab 500 HV), um eine höhere Anpassungsfähigkeit an den Gegenkörper zu ermöglichen. Diese zähere DLC-Schicht kann vorteilhaft sein, wenn ein gewisses “Mitgehen” der Schicht bei Verformung oder Stoßbelastung gewünscht ist.
"Dicke" Schichten
Während Standard-DLC typischerweise 1–3 µm dünn ist, können DLC Xtended-Schichten deutlich stärker aufgebaut werden. Üblich sind 5–15 µm; in speziellen Fällen sind sogar 20–30 µm Schichtdicke realisierbar. Solche Dickschichten bieten erhöhten Korrosionsschutz und eine längere Standzeit, da mehr Schichtvolumen für Verschleiß zur Verfügung steht
Einlaufschicht
Um das Reibungsverhalten insbesondere in der Einlaufphase und bei häufigen Start-Stopp-Zyklen weiter zu optimieren, hat RÜBIG eine dünne Einlaufschicht entwickelt. Hierbei wird auf die harte DLC eine ca. 0,5 µm dünne, weichere Deckschicht mit leicht modifizierter Chemie aufgebracht. Diese opfert sich während der Einlaufzeit ab und passt sich an die Gegenfläche an. Das Ergebnis ist ein deutlich verbessertes Einlaufverhalten und nochmals reduzierte Reibwerte im Dauerbetrieb (Reibungskoeffizient gesenkt auf ~0,03). Danach wirkt die darunterliegende harte DLC-Schicht voll weiter.
Hartchrom
DLC Xtended® ist die ideale Lösung als Ersatz für Hartchrom auf hochbelasteten Bauteilen. Typische Anwendungsfälle sind z.B. Hydraulikzylinder-Stangen, Kolben und Komponenten im Maschinen- und Anlagenbau, die bislang hartverchromt wurden. Auch in der Automobiltechnik (etwa für Motorenteile, Ventiltriebe oder Einspritzkomponenten) und im Werkzeug- und Formenbau kommt DLC Xtended zum Einsatz, wenn sowohl Verschleißfestigkeit als auch Korrosionsschutz gefordert sind. Dank der Duplex-Technologie werden die typischen Anforderungen von Hartchromschichten erreicht oder übertroffen – bei gleichzeitig verbesserter Umweltbilanz (kein Chrom VI).
Unsere Dlc-Beschichtungsanlage
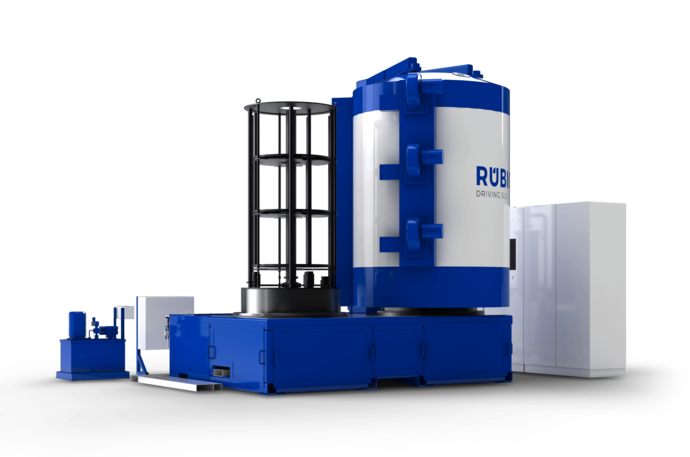
Diamond Xtended
Mit der MICROPULS® Diamond Xtended liefert RÜBIG eine der innovativsten Anlagenlösungen im Bereich der DLC Beschichtungstechnologie.