DLC Xtended® –
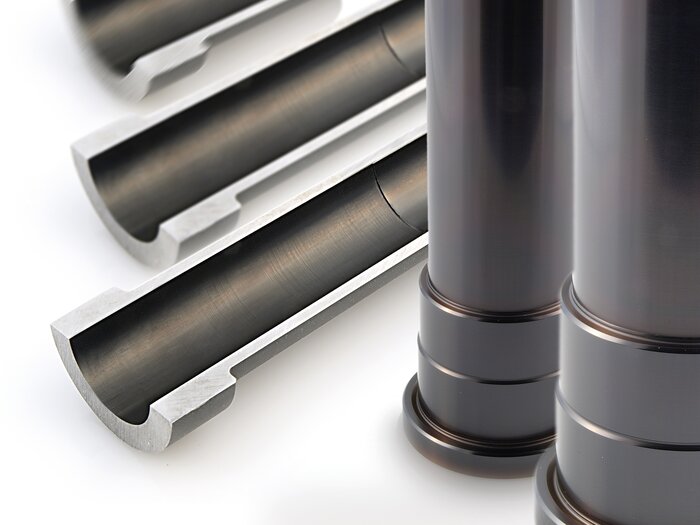
With DLC Xtended®, RUBIG presents an innovative Chromium 6 replacement technology that serves as a full-fledged substitute for hard chrome coatings (Chromium VI, Cr VI) in hydraulic cylinders, mechanical engineering, and OEM components. Hard chrome layers produced from Cr-VI-containing electrolytes were long considered the standard for wear and corrosion protection, but today they face heavy criticism due to significant health risks and strict regulation. Chromium(VI)-compounds are classified as carcinogenic, and its use in the EU is fundamentally banned unless a complex exemption (REACH authorization) is granted. Starting 2026/2027, further restrictions on Chromium(VI) are expected – thus more and more decision-makers are seeking a hard chrome replacement that is technically equivalent and poses no Chromium(VI) issues. RUBIG’s DLC Xtended® is exactly this Chromium 6 alternative, combining expertise with proven practical performance.
Parameter | Hard Chrome / Chromium 6 | DLC Xtended® (hard chrome replacement) | Note |
---|---|---|---|
Coating thickness | Decorative: < 1; Functional: 2–1000 µm | Duplex coating: approx. 10–20 µm | Varies greatly depending on application |
Hardness | 600 – 1200 HV | 500 – 1500 HV | |
Friction coefficient (µ) | - | µ ~ 0.05 (dry against 100Cr6) | Very low friction; with appropriate roughness, beneficial for sealings |
NSS test duration (corrosion resistance) | 20 µm Cr: 24–120 hours; 10 µm Ni + 20 µm Cr: up to 500 hours | Up to 1000 hours (with good surface quality) | Measure of corrosion resistance |
The above mentioned coating properties were achieved under ideal conditions. Depending on surface condition, component size, material, and other factors, the properties on the actual part may vary.
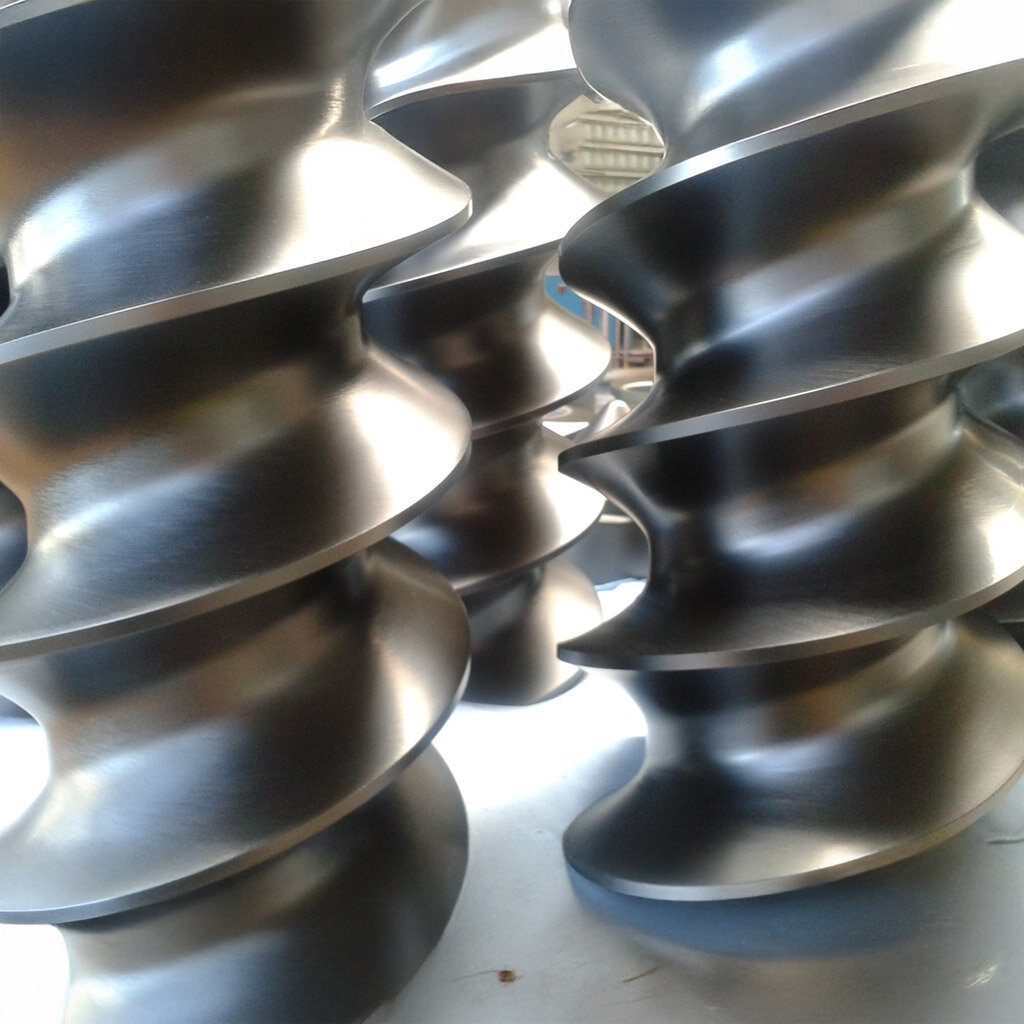
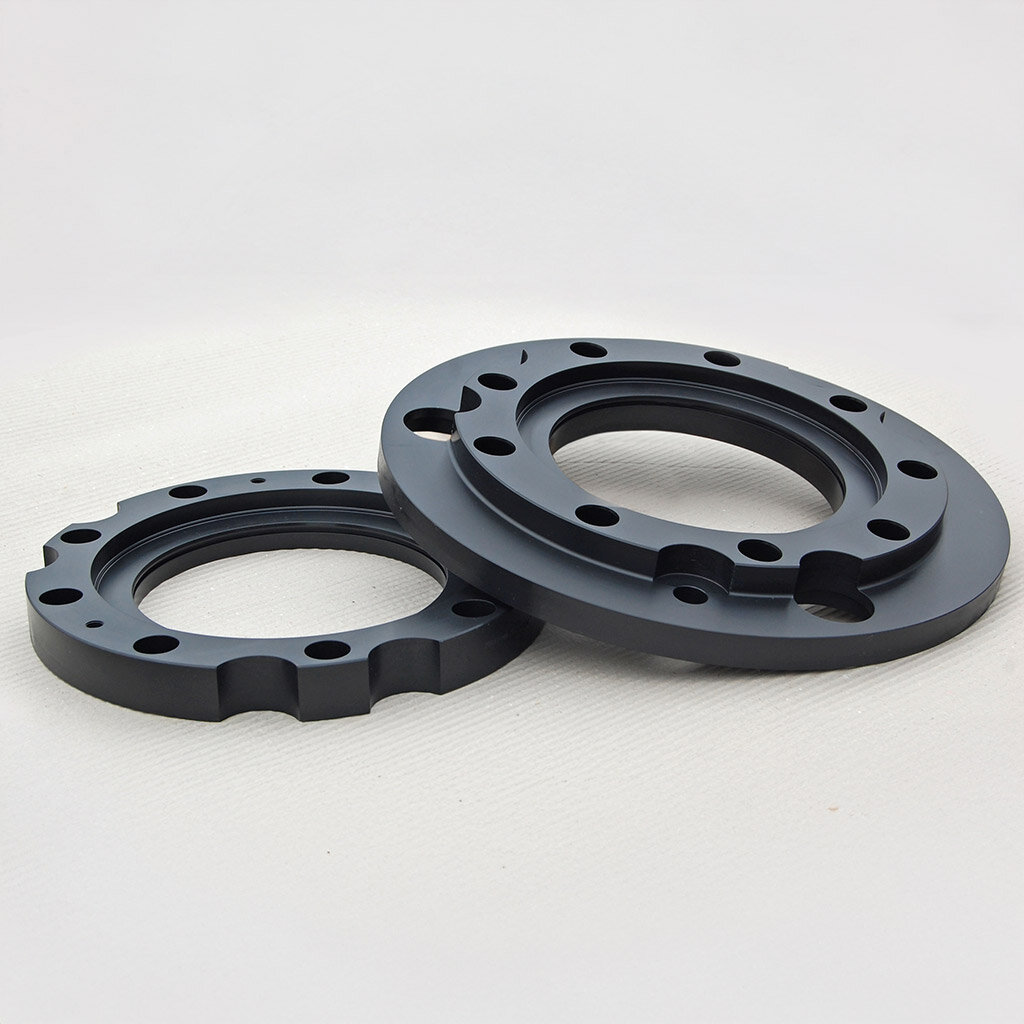
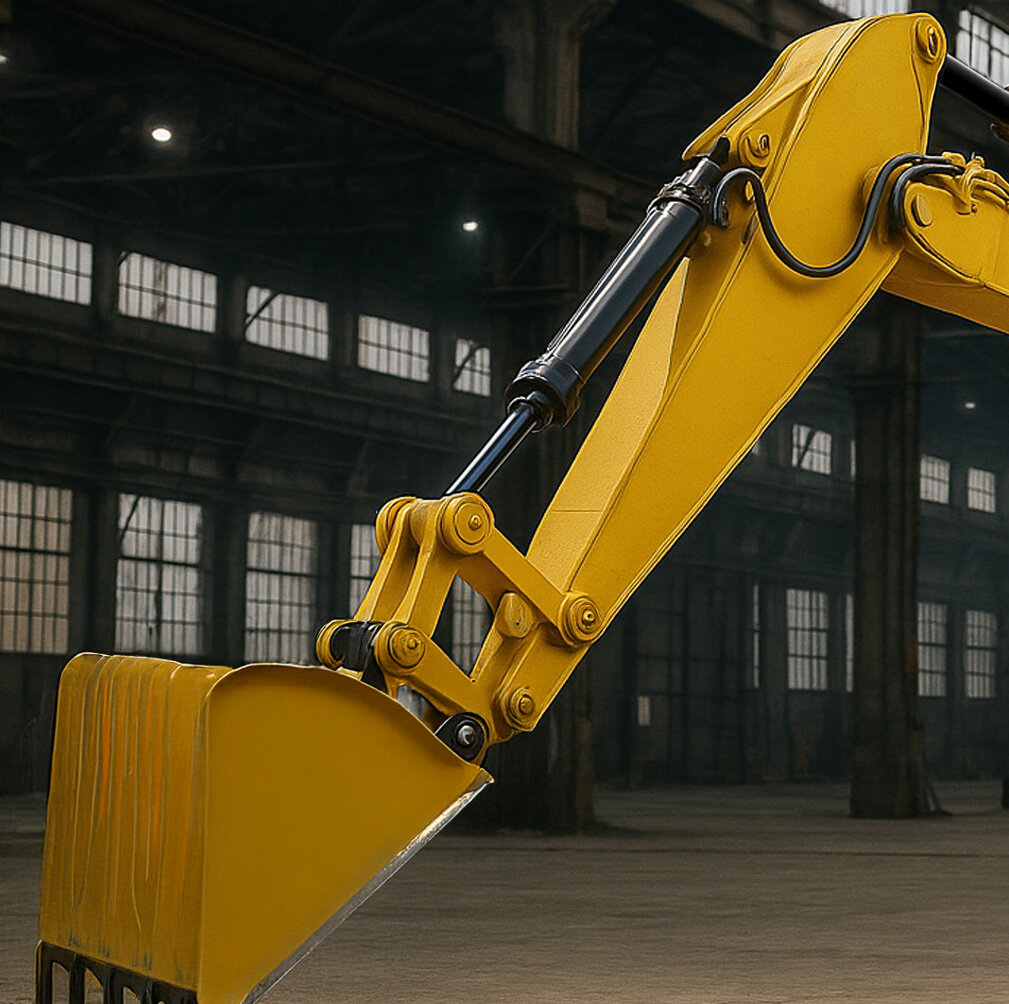
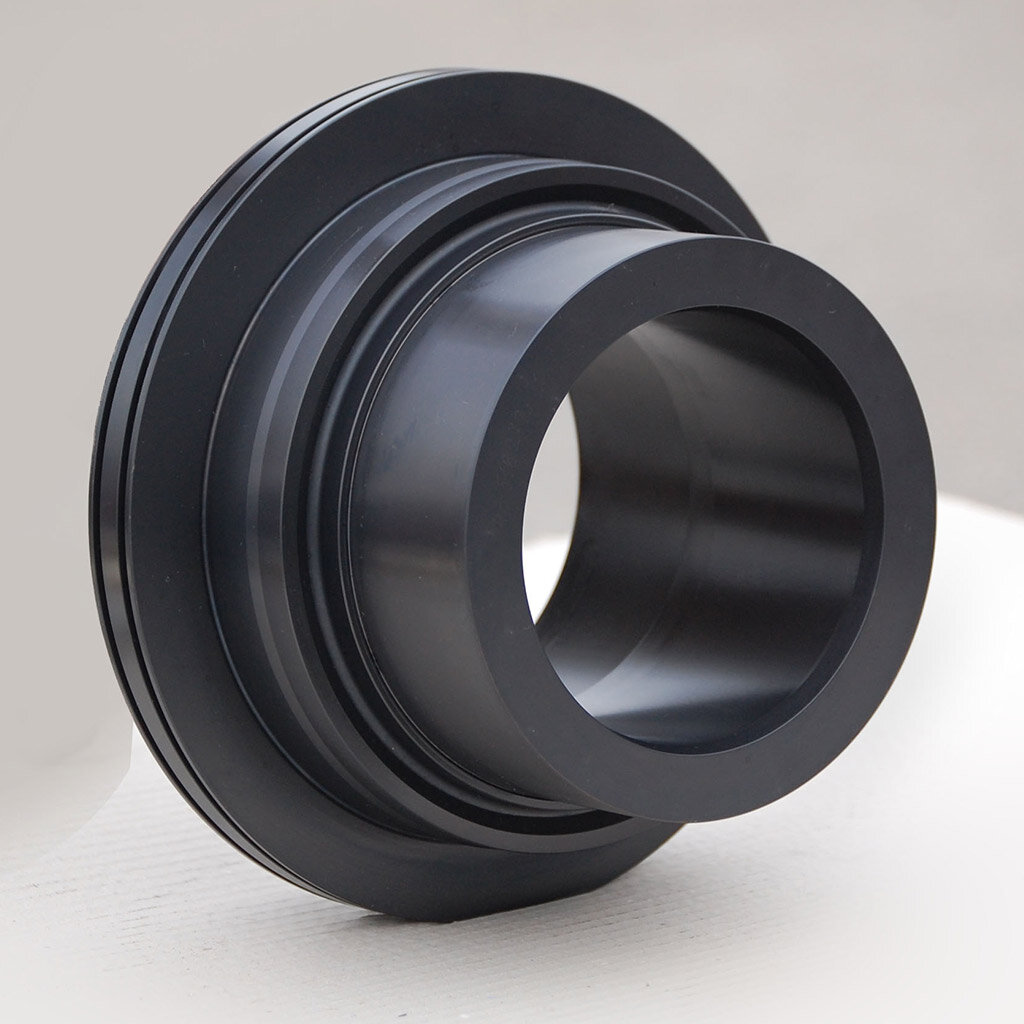
Why Chromium 6 Is Problematic
Electrolytes containing chromium trioxide (CrO₃) and sulfuric acid are used for hard chrome plating. The aerosols of this Cr(VI)-bearing electrolyte generated during the plating process are toxic and carcinogenic. Accordingly, the EU introduced strict exposure limits and since 2017 has allowed the use of Chromium(VI) with special authorization only. The necessary exemptions under REACH are extremely burdensome – each application requires hundreds of pages of documentation (substance description, substitution plan, socio-economic justification, etc.). Despite these hurdles, the largest industry-wide authorization (CTAC) was annulled by a court in 2023, further increasing uncertainty in the industry. Many coating providers hesitate to invest, yet regulatory pressure is forcing the search for alternatives. From a safety and legal standpoint, Chromium 6 is on its way out – and companies urgently need a future-proof solution.
Advantages of DLC Xtended®
over Hard Chrome
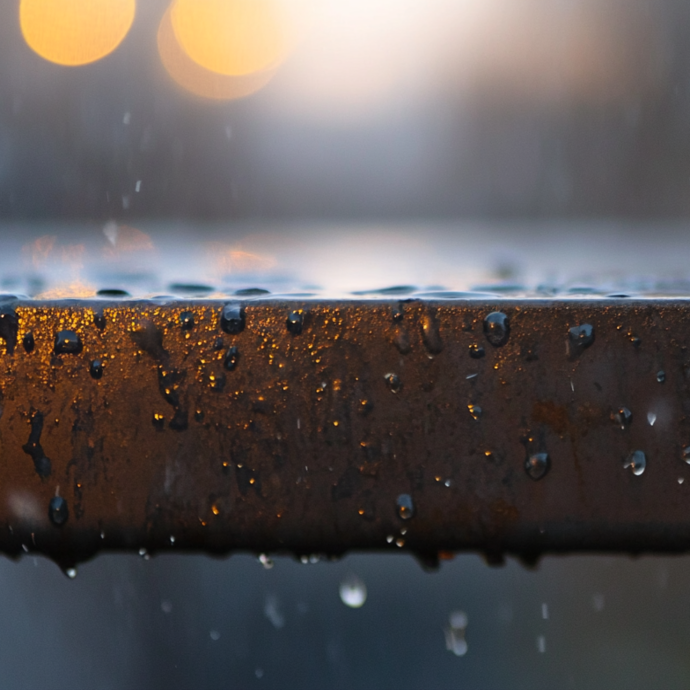
Permanent protection against rust
A central criterion for piston rods and similar components is corrosion protection. DLC Xtended® delivers outstanding results here – without the use of Chrome VI. In neutral salt spray tests (NSS per DIN 9227), DLC Xtended®-coated piston rods achieve up to 1000 hours of resistance with no or only minor corrosion (under ideal conditions). To reach these values, the required surface quality must be achieved prior to coating.
This Chrome(VI)-free coating thus meets even the highest industrial requirements, which previously were only attainable with nickel-chrome layers. Studies show that for the most demanding applications (e.g. >500 h NSS), a duplex DLC Xtended® coating is recommended. Compared to conventional hard chrome, the DLC layer forms a more dense, continuous surface without the micro-cracks typical of electroplated chrome . This provides reliable corrosion protection without Chrome VI.
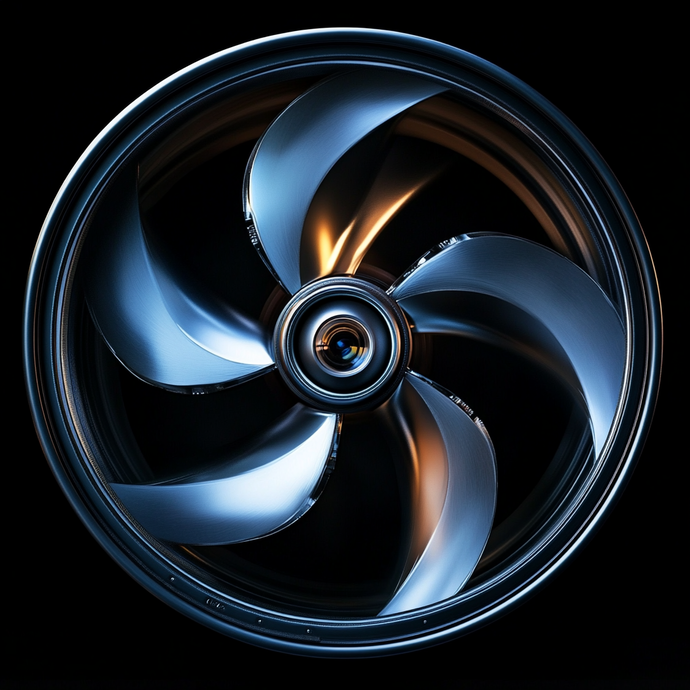
Reduced friction and less wear
DLC Xtended® is characterized by a very low coefficient of friction (μ < 0.05 against steel, given appropriately low pre-set roughness). This low-friction surface brings two benefits: On the one hand, it greatly reduces direct wear on the component itself – the coating shows virtually no abrasion in operation. On the other hand, the low friction protects all counterpart parts such as sealins in hydraulic cylinders. Tests with typical hydraulic sealing systems (PTFE “Stepseal®”) demonstrated that DLC Xtended® causes similarly minimal sealin wear as hard chrome, and does so without any measurable coating wear.
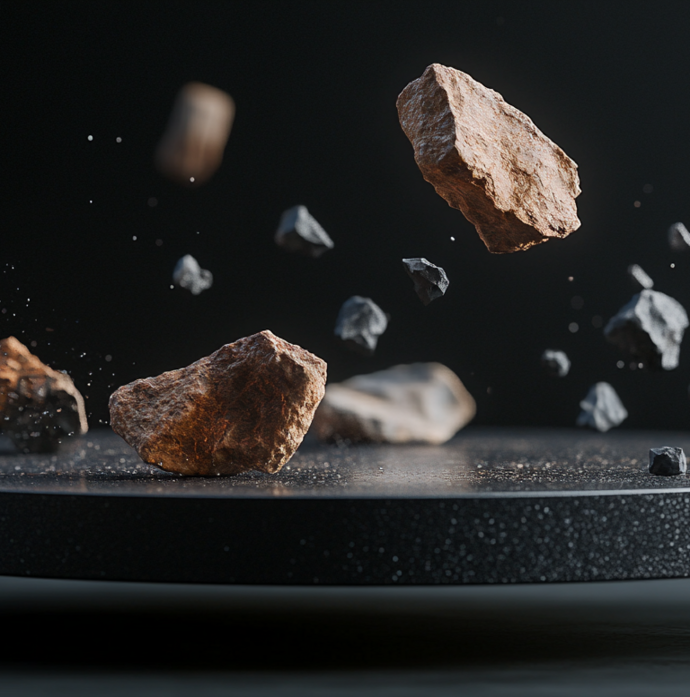
Highest surface quality and hardness
The surface finish of DLC Xtended® is especially smooth and fine when the incoming surface has low roughness. Typical roughness values are in the range of Ra 0.1–0.2 µm – thus the coating meets the strict requirements for hard-chrome surfaces in sealing contact areas. Unlike galvanically deposited chrome, DLC exhibits no microporosity or crack networks. The coating forms a homogeneous film that gives the component a uniform anthracite-black finish. This smooth surface reduces friction (as described above) and also makes cleaning easier : dirt, residues or deposits can be removed easily, since the DLC coating has non-stick properties. Furthermore, DLC Xtended® (hard chrome replacement variant) achieves a hardness up to 1500 HV, which is on the level of or higher than hard chrome. The plasma nitriding step included in the coating process provides a good supporting effect for the coating.
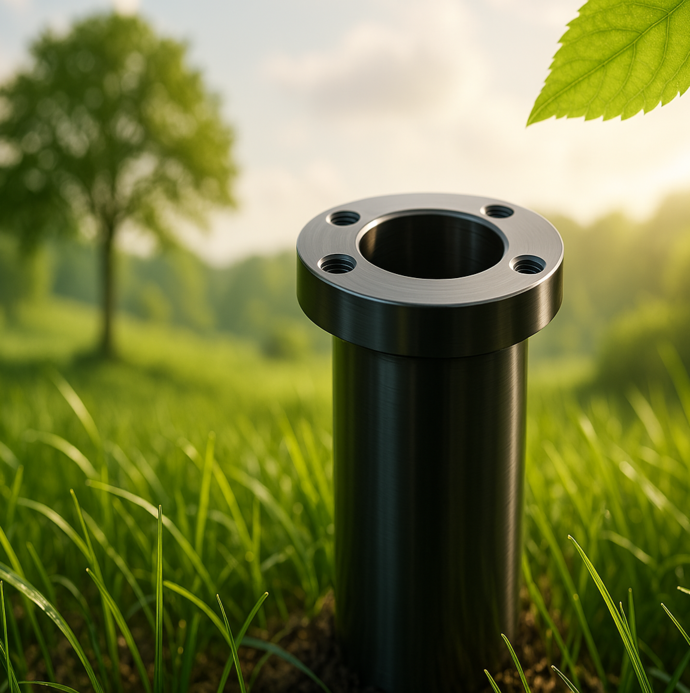
Future-proof
With DLC Xtended®, you are relying on an environmentally friendlycoating technology that works without toxic chemicals. In contrast to hard chrome electroplating, no chromic acid wastewater or Chromium(VI) -loaded sludge is produced that would need to be disposed of as hazardous waste. This significantly reduces environmental impact – no Chrome VI means no danger to employees, no cancer risk, no Chromium(VI) emissions into air or water. Instead, the DLC process runs in closed plasma systems under vacuum; emissions and energy consumption are low. This also pays off for your company in terms of compliance: you will meet current and future regulations with ease.
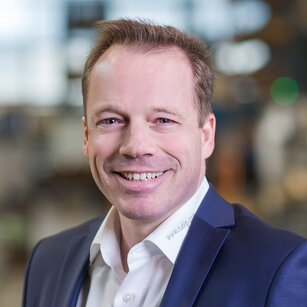
Switch Now
The time is ripe to turn your back on hard chrome and embrace RUBIG’s advanced DLC Xtended® technology.
DI David Unterberger
Head of Sales – Heat Treatment
Hydraulics industry:
The future is “Cr(VI)”-free
Corrosion and wear protection, high surface hardness and low roughness: piston rods for hydraulic cylinders are among the main products in fluid technology that must meet these requirements. Until now, the hydraulics industry relied on hard chrome coatings to achieve these properties.
How can we help?
We are happy to advise you personally. Contact us and get detailed information about the coating you want!
Our Dlc coating system
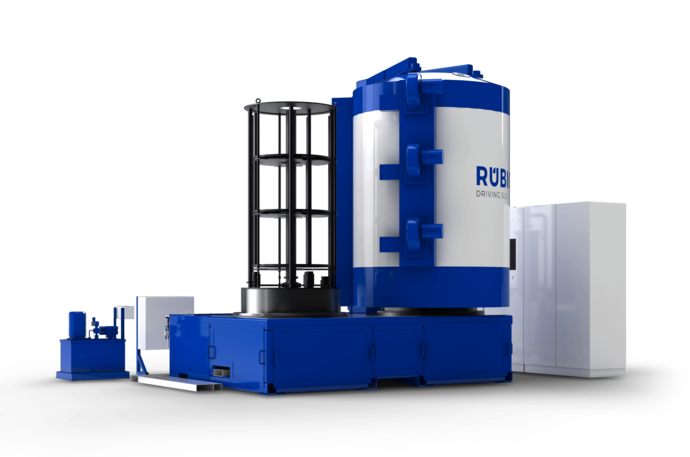
Diamond Xtended
With the MICROPULS® Diamond Xtended RUBIG supplies one of the most innovative system solutions in the field of DLC coating technology.
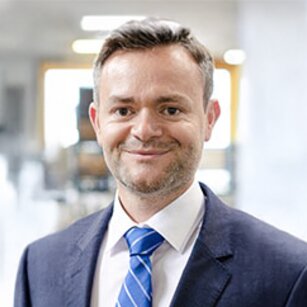
Innovative and Tailor-Made
With over three decades of technological leadership, we develop equipment solutions precisely tailored to your manufacturing processes. Consult with our experts to implement a solution that sustainably optimizes your production.
DI Stefan Haas
Head of Sales - Industrial Furnaces