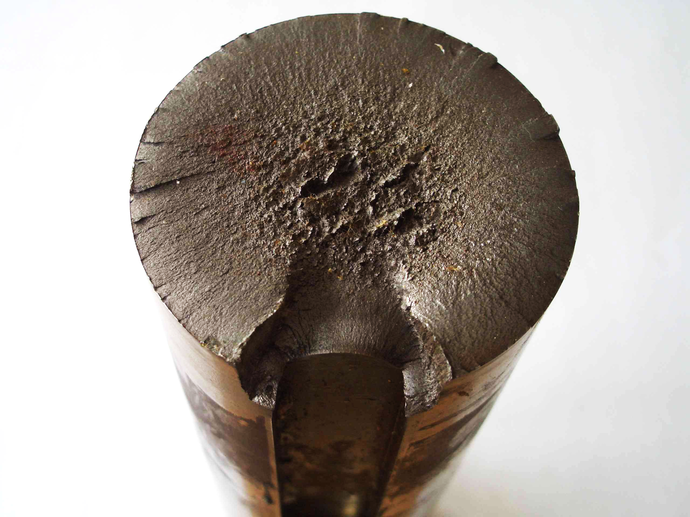
Failure analysis
Our expertise enables us to identify damage mechanisms and to determine the causes of damage. Based on these findings, we derive measures for damage prevention. With our comprehensive know-how, we support you in ensuring stable and high-performance components in the long term.
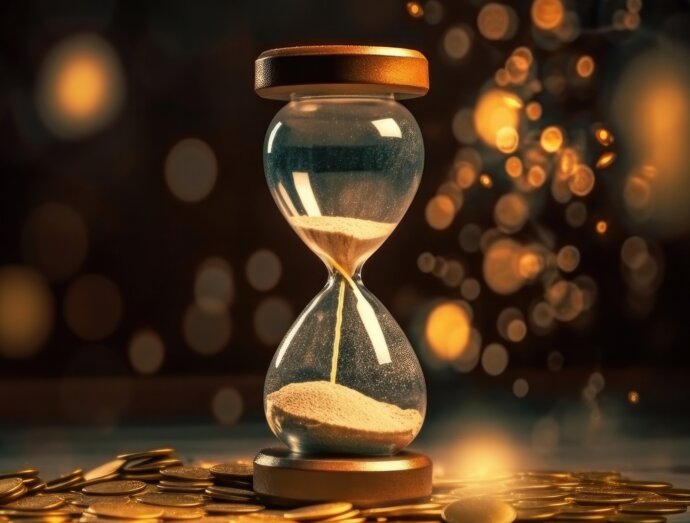
Save time and money
Practice shows that every mistake that can theoretically happen will also occur at some point and will be repeated, provided that nothing has been done about the causes of the mistake. Therefore, it is expedient to systematically determine the causes of errors and consistently eliminate them.
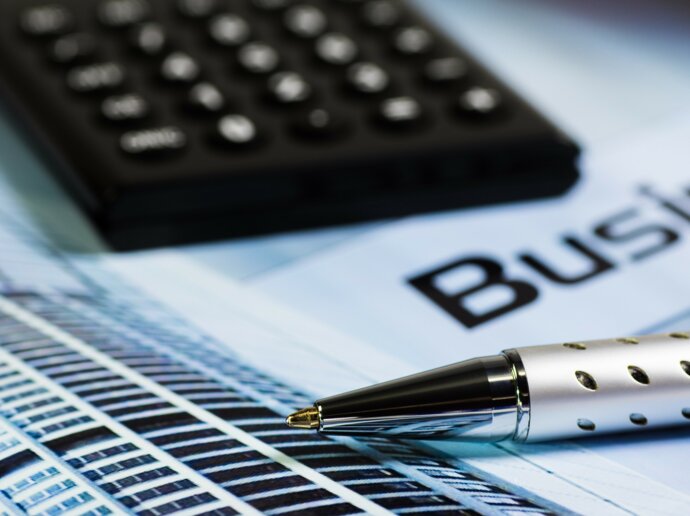
Our tip
Avoid the use of "trial & error" as well as hasty measures for future damage prevention. These approaches often prove to be ineffective. Through a systematic failure analysis, you will gain valuable knowledge about defective components and can initiate positive changes in a targeted manner in order to prevent repeat errors. This opens up a promising path for you to achieve optimal results.
Systematics of failure analyses
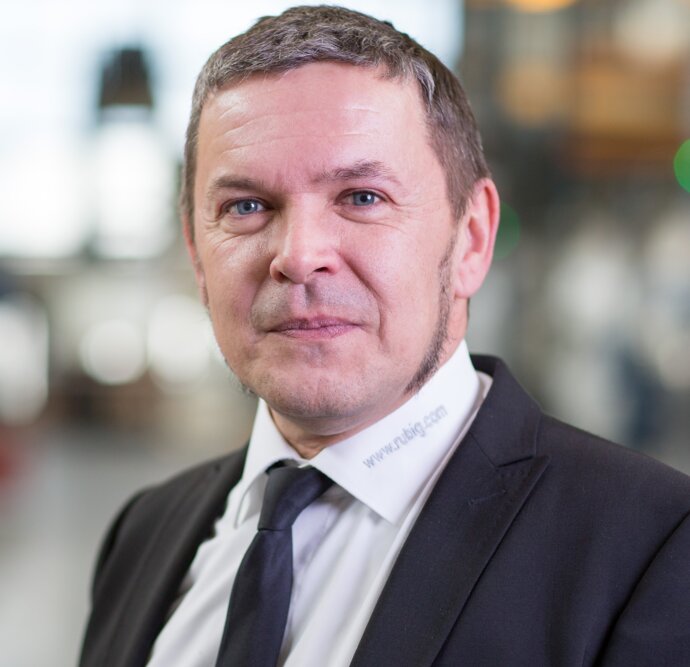
Assessment of material, process or application-related damage to metallic components and tools, determining and limiting the causes and deriving suitable, appropriate and practicable prevention measures for
- cracks and fractures
- wear and tear
- corrosion
- combined damage mechanisms, e.g. fracture due to hydrogen embrittlement, stress corrosion cracking, surface fatigue due to fretting rust etc.
Personal Consultation
Do you need help with the analysis of your components? Contact us!
Our materials service team is ready to carry out a thorough inspection of your components.
Assessment of material and heat treatment conditions of defective components and tools:
- Target/actual comparison with the specifications (conformity check)
- Evaluation of whether the material and heat treatment condition determined for unknown components is typical, reasonable, suitable for this application
- Assessment of defects in steel production and pre-material production
- Assessment of manufacturing-related defects, such as friction martensite, grinding burn, forging and casting defects, welding defects, eroding defects, defective heat treatment
- Assessment of whether detected defects or deviations represent a typical variation or whether the load-bearing capacity of the component has actually been reduced as a result of the damage in the specific case