These coatings are used in various applications, from medical technology to food packaging to construction and textile materials.
At RUBIG we offer copper coatings and NitroPep coatings.
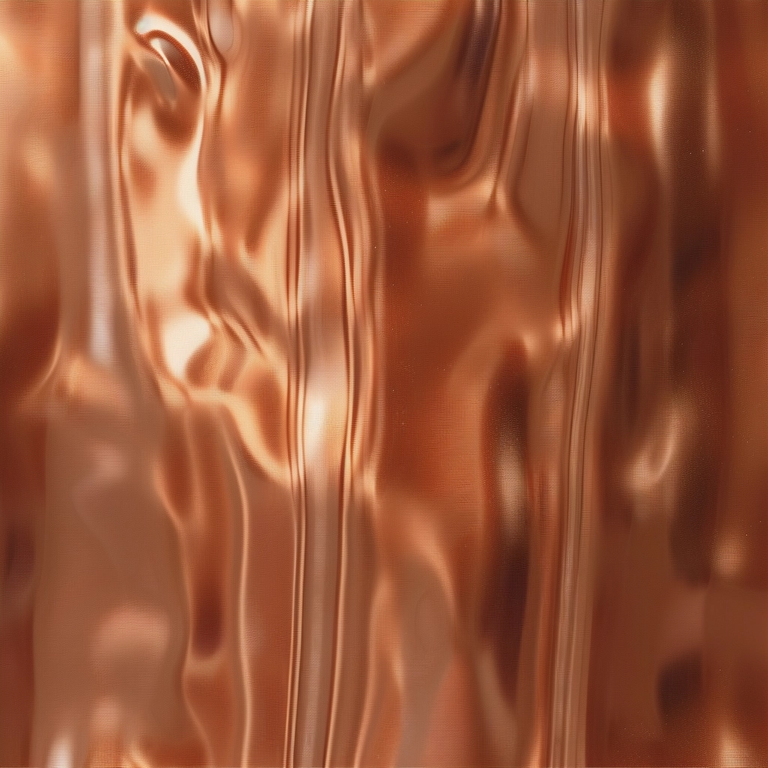
Copper
Copper has a natural, antibacterial and antiviral effect. With the coating based on copper or copper oxide RUBIG AntiViralCoating the spread of viruses and bacteria can be reduced or even prevented.
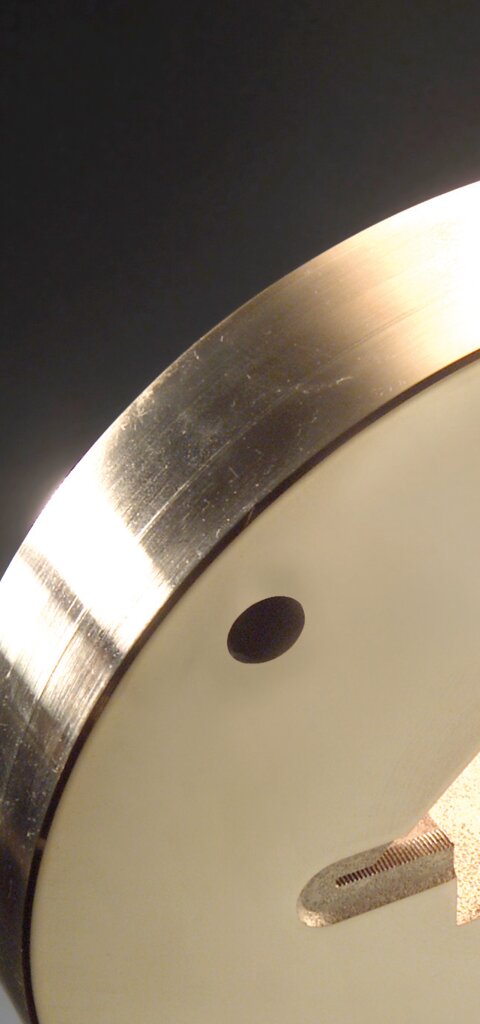
How does the coating work on components?
The effect against bacteria and viruses is created by the oxidation of the surface. Components made of metal, plastic or filter materials can be coated. The filters, in turn, can be made of non-woven fabric or foam.
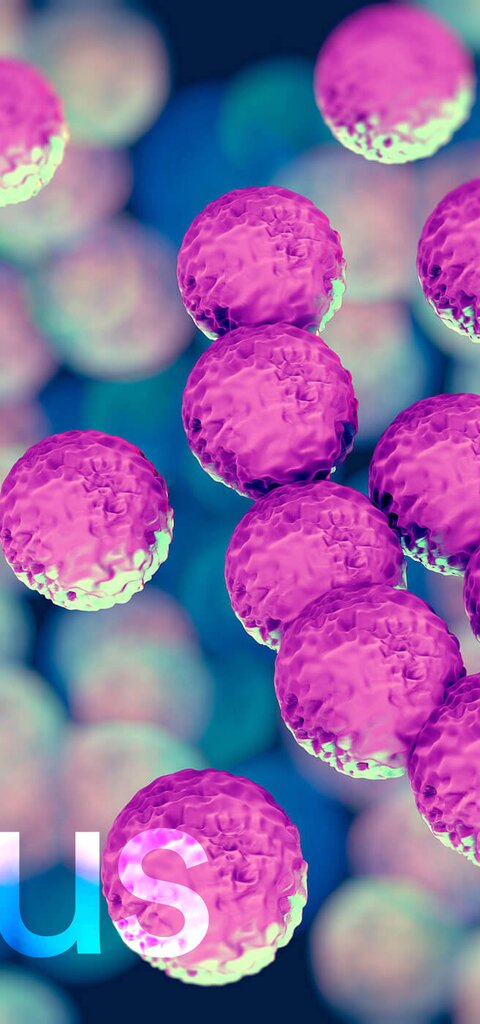
Do coatings differ depending on the strains of viruses and bacteria?
Properties such as service life, effectiveness and haptics can be influenced by the targeted alloying of chemical elements. The coating type can be adapted to the corresponding customer requirements and the coating system is also constantly being further developed.
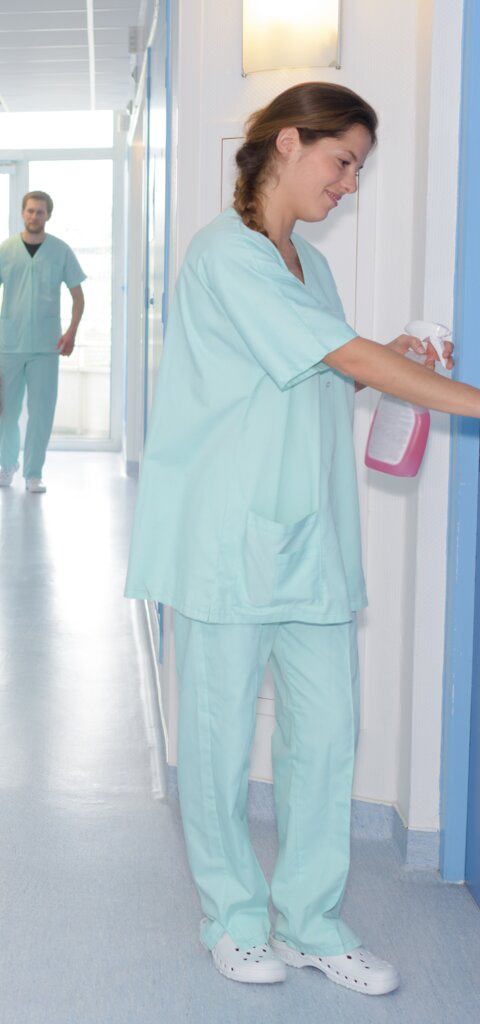
What is the typical field of application of a biocidal coating?
Biocidal coatings of copper or copper oxide are ideal for keeping surfaces germ-free in highly frequented places in public spaces. The spread of viruses and bacteria can thus be effectively reduced. Typical areas of application are handrails, door handles or grab handles.
How can we help?
We are happy to advise you personally. Contact us and get detailed information about the coating you want!
Nitropep
Effective protection against viruses and bacteria
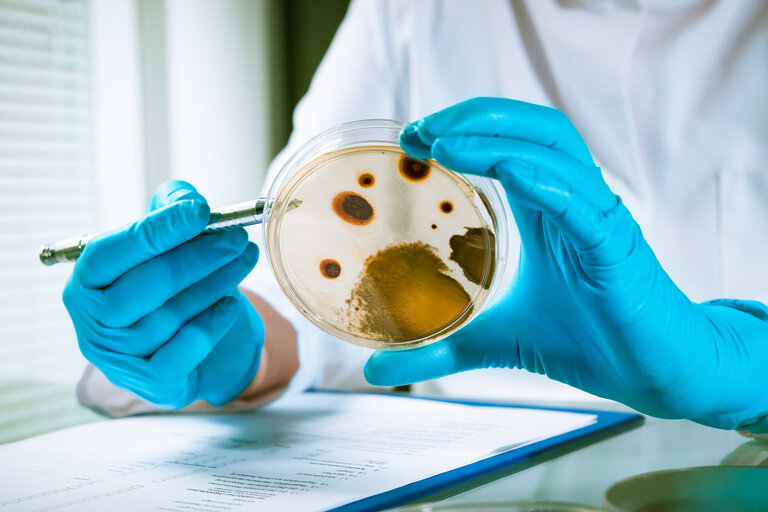
RUBIG NitroPep is a biocide-approved coating in the EU that efficiently eliminates pathogens on contaminated surfaces.
To achieve this, disinfectant and antimicrobial agents, such as chlorhexidine, are included in the coating. As a result, the coating prevents both individual and mixed populations of microorganisms from settling on surfaces in biofilms. This means that there can be no recontamination of the surface and the coated surfaces remain germ-free.
The coating process takes place at room temperature and is therefore suitable for a wide variety of materials such as metal or plastic.
The effect is scientifically confirmed
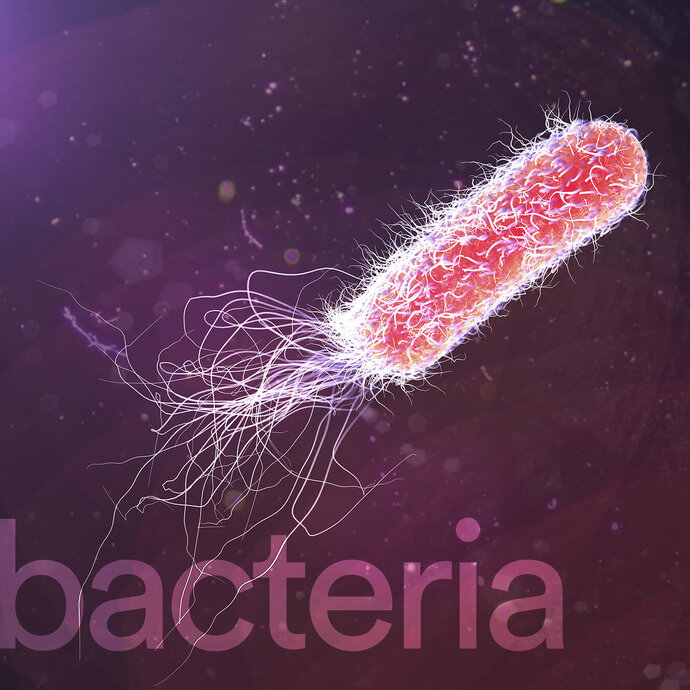
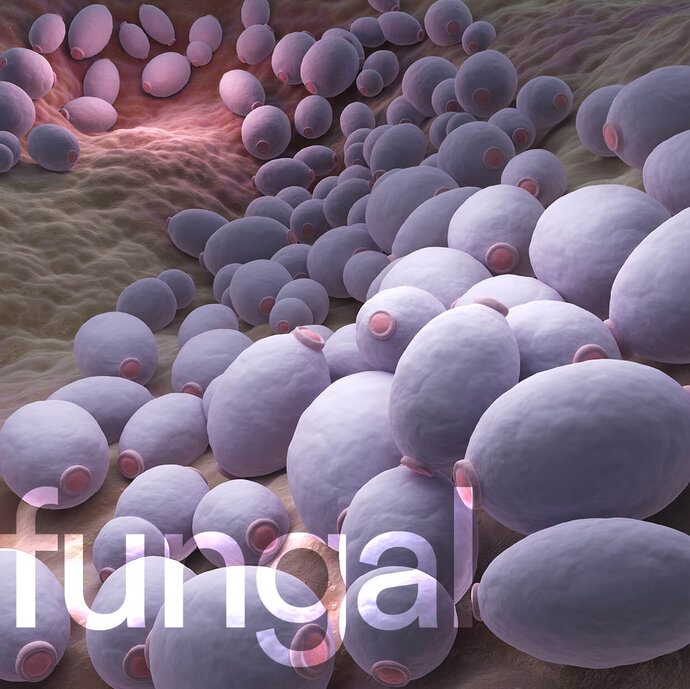
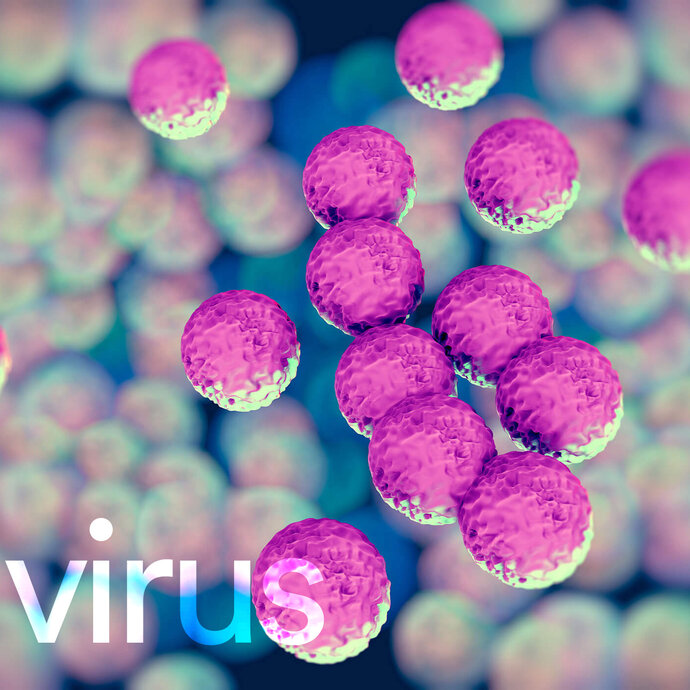
NitroPep was developed by researchers at the University of Birmingham. The advantages of this coating are the destruction of pathogens such as viruses and bacteria by physical means and the effectiveness against antimicrobial-resistant pathogens. This effect has been scientifically tested and confirmed.
NitroPep is a non-toxic, antibacterial coating and is suitable for:
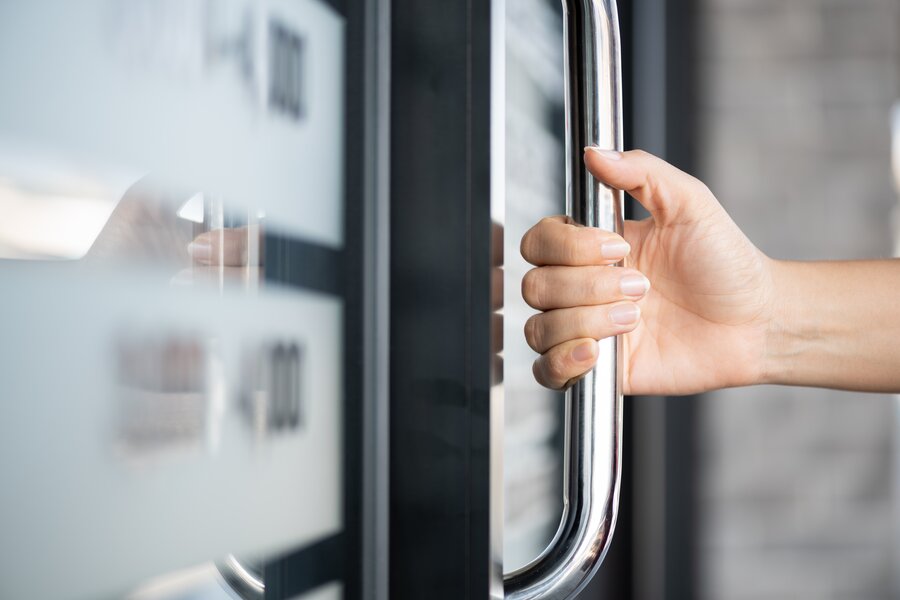
Door and grab handles
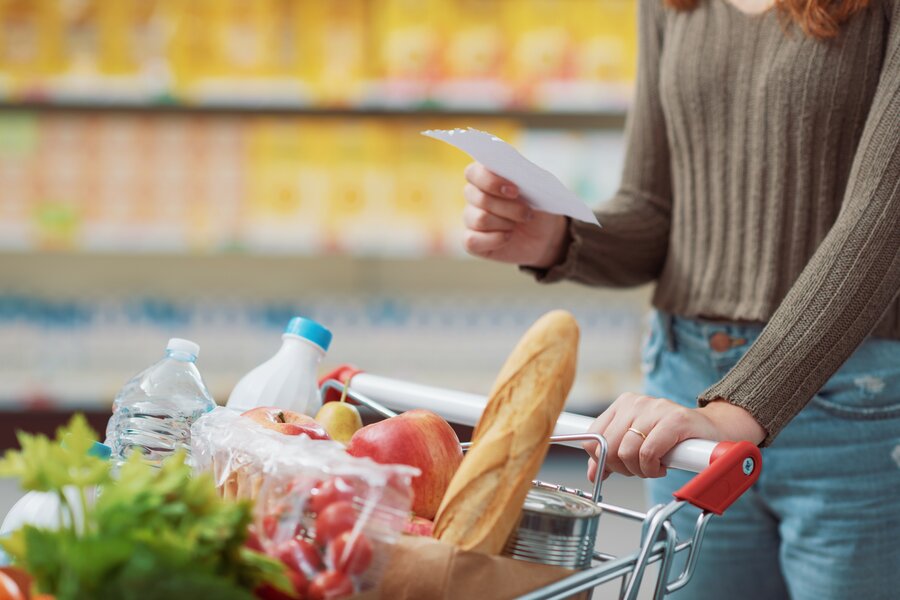
Handle protection for shopping carts
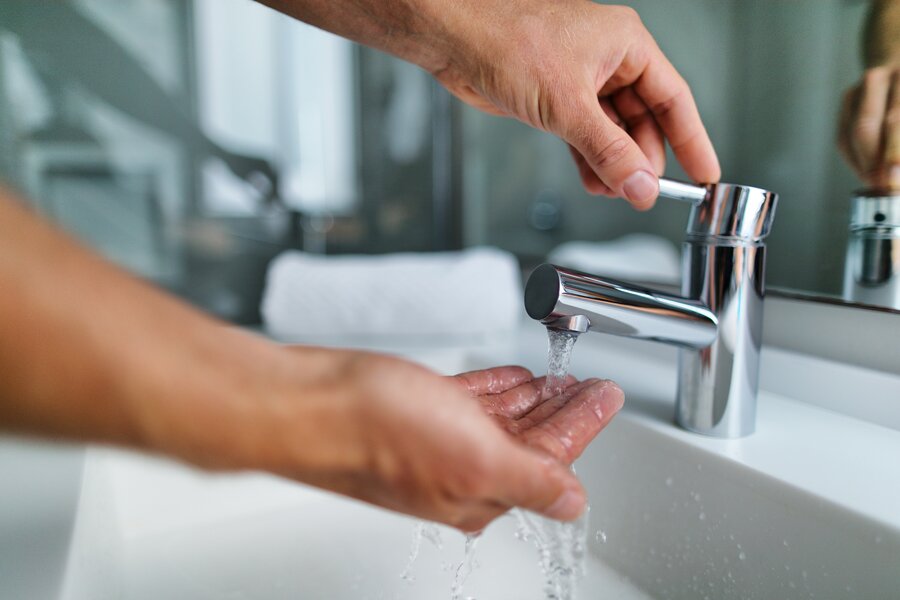
Sanitary fitting
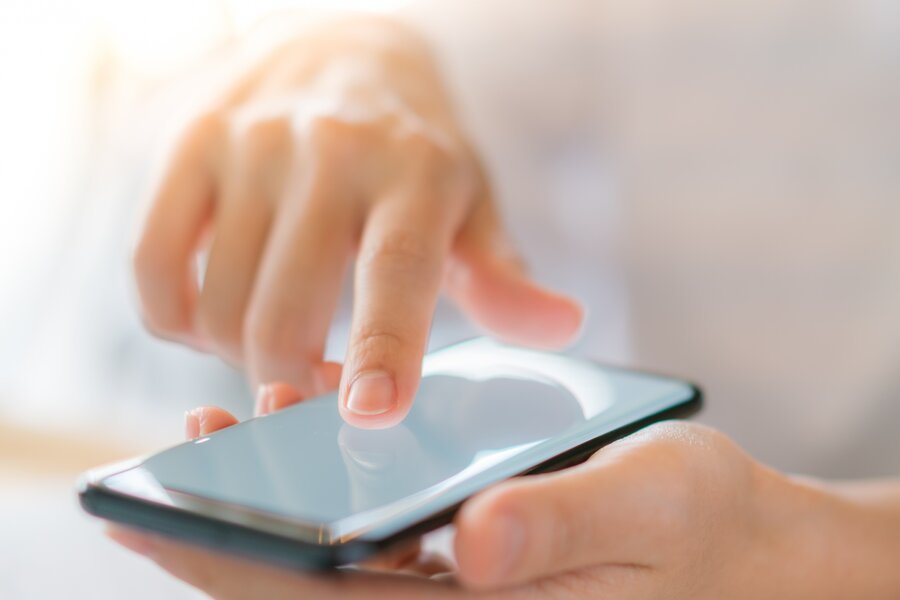
Display films
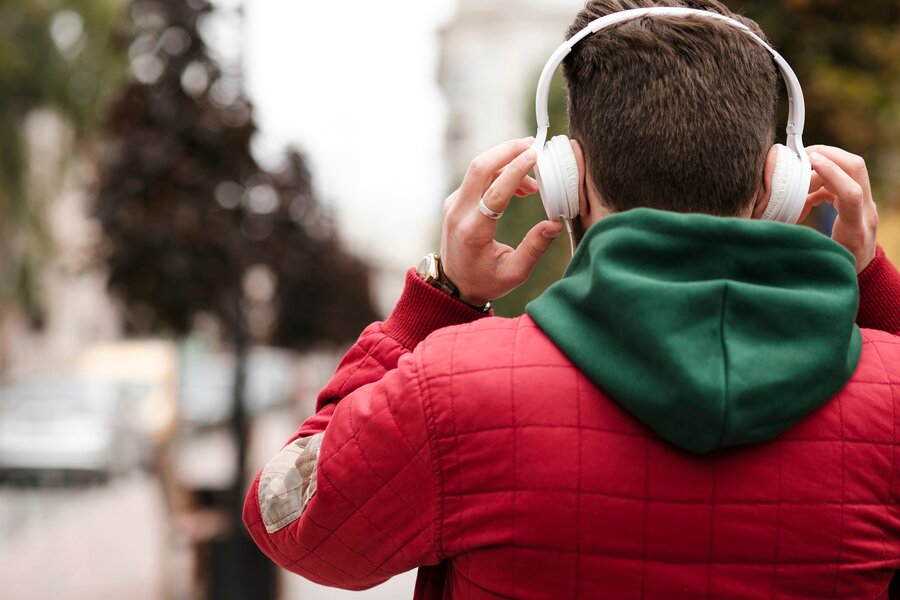
Headphones
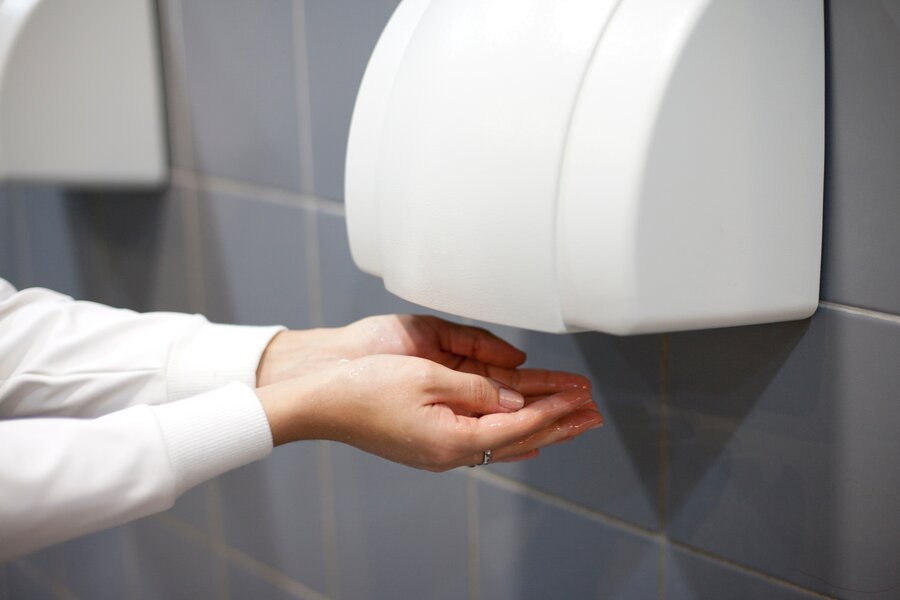
Hand dryers
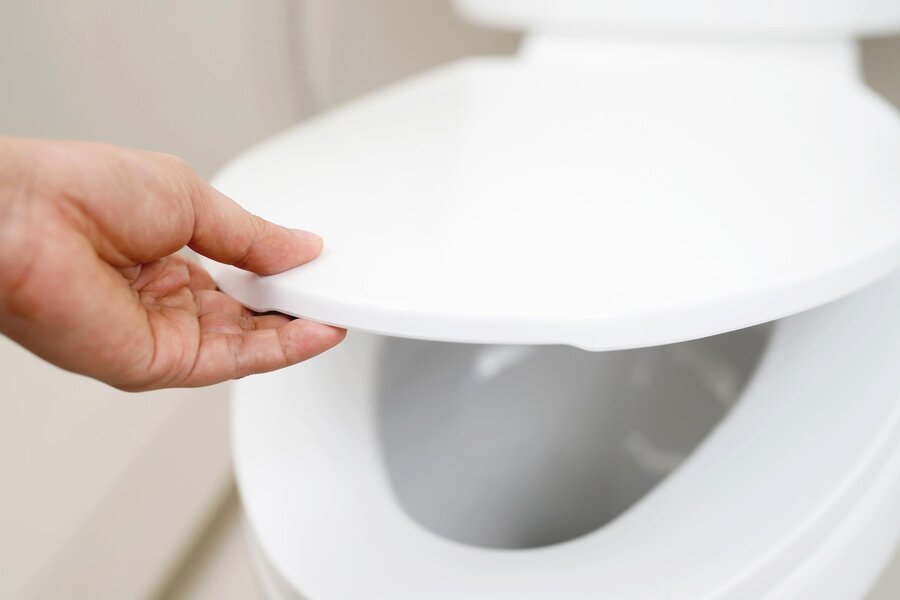
Toilet seats
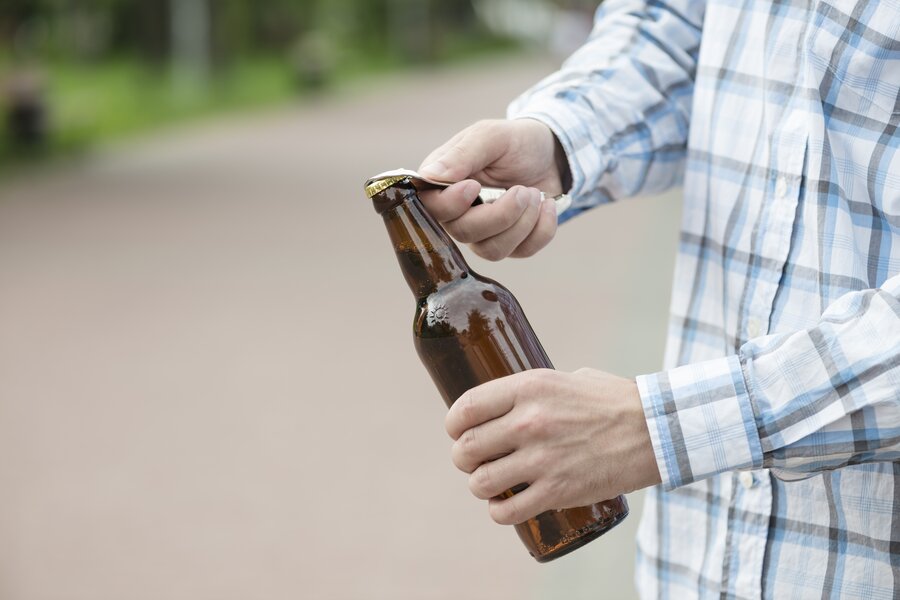
Bottle openers
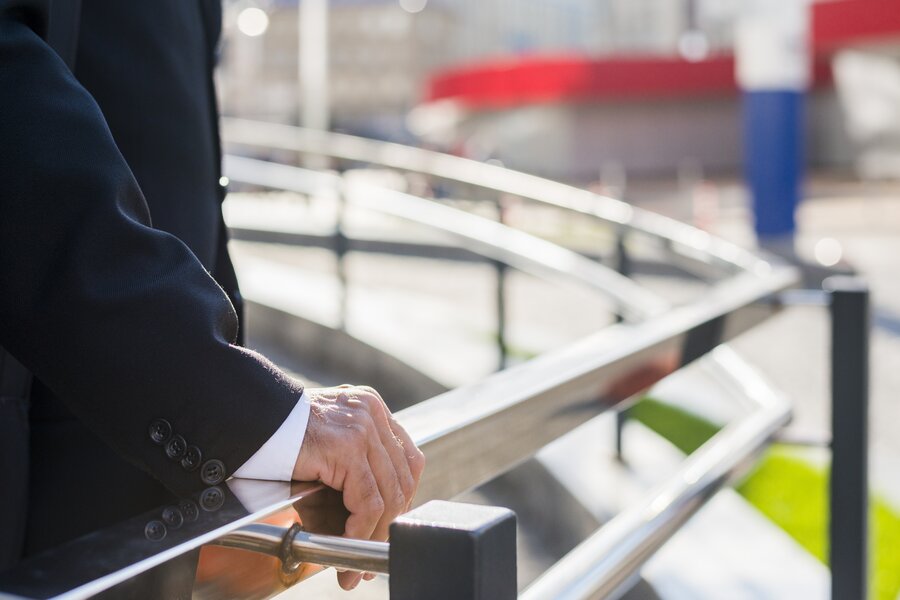
Handrails
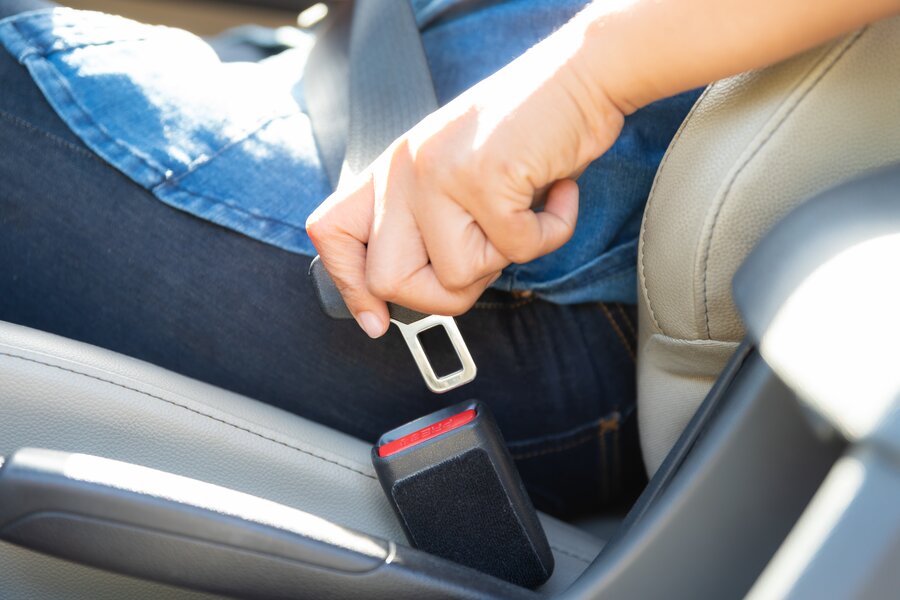
Belt buckles
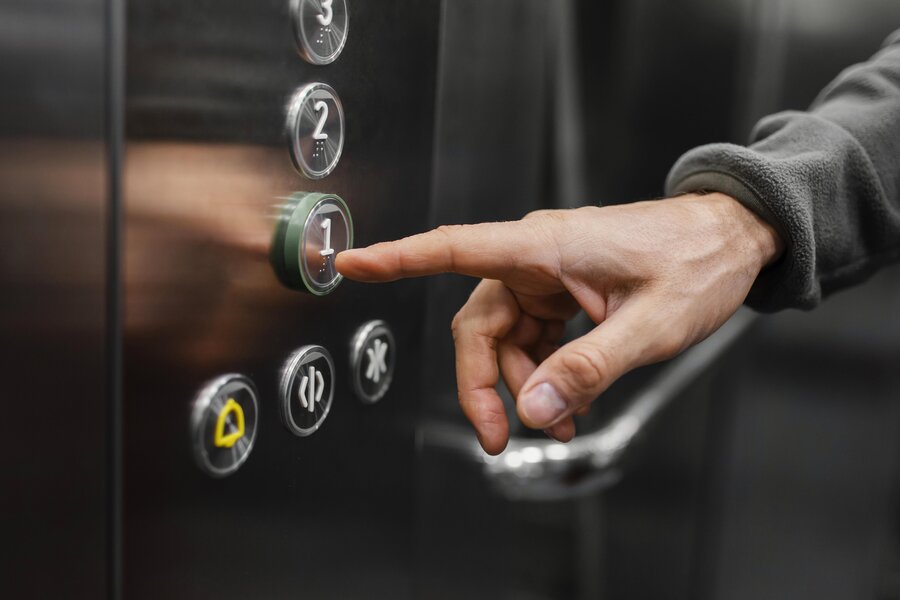
Buttons
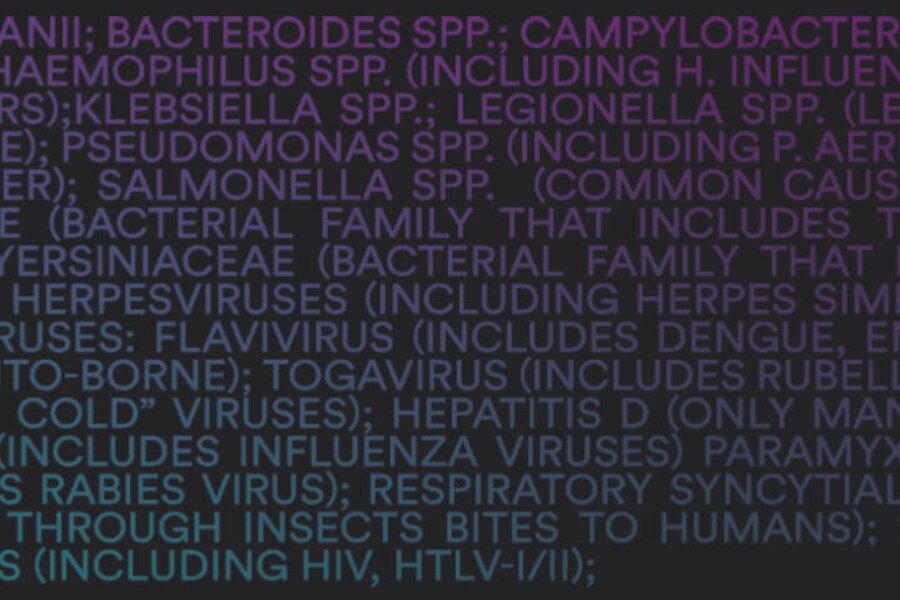