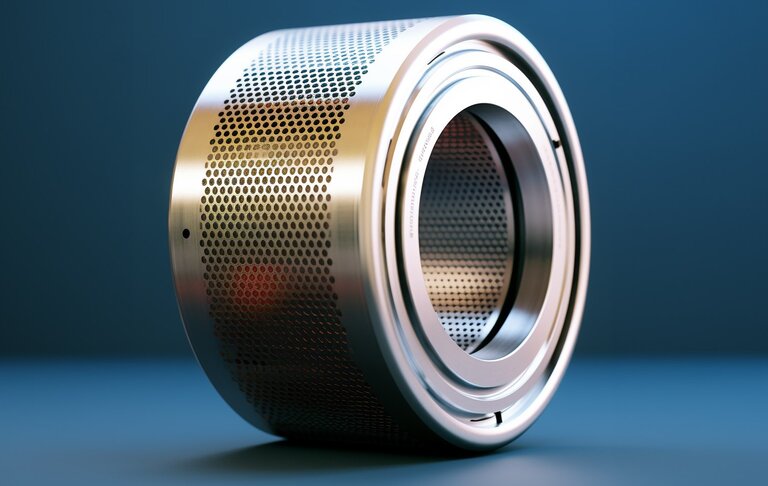
TiCN
The multi-layer coating system based on titanium carbonitride reduces friction and abrasive wear during forming processes and thus enables significantly longer service lives. As a coating of forming tools, it improves the forming behavior and the surface quality of the produced parts. TiCN is even harder than the TiN coating and is recommended for all tools that are exposed to a high wear load.
Gold lf Plastit®
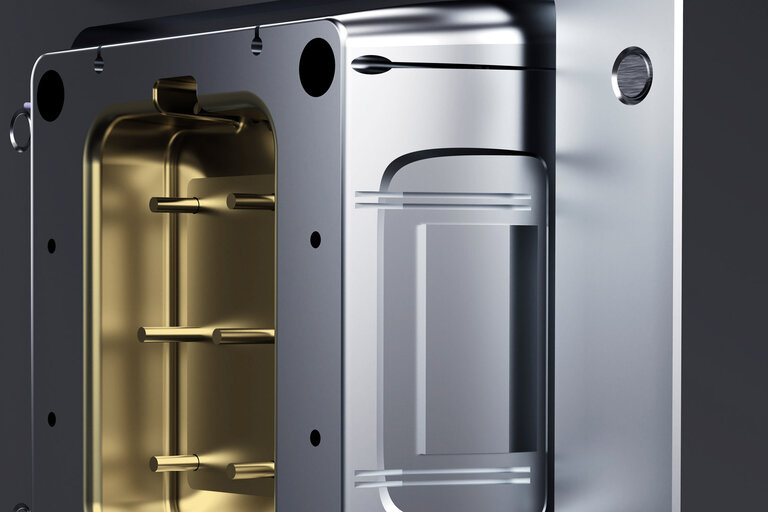
TiN
The gold-colored, attractive titanium nitride coating has long been a universally proven standard coating with balanced properties:
- High hardness and adhesive strength
- Good chemical resistance
- Good temperature resistance in air
- Relatively low thermal conductivity
- Low friction coefficients (< 0.2 ) compared to steel
- Biocompatible and food safe
It is characterized in particular by its high toughness and extremely low tendency to cold welding, and it insulates against corrosion. The golden coloration makes the beginning of any wear and tear of the coating recognizable at a glance. The first choice for tools in plastics processing.
Titanium-based coatings are particularly used in the aerospace, automotive and medical technology sectors.
Boron Nanocomp Plastit®
TiBN
When casting aluminum alloys in permanent molds, the molding tools are stressed by erosion, corrosion, sticking and thermal fatigue. As a result, the surface quality of both the tools and the castings produced deteriorates. Our BORON Nanocomp PLASTIT®, a multilayer coating with varying boron contents and many advantages for tools, cores and ejector systems, protects against these stresses:
- Increase of wear resistance
Reduction of corrosion by aluminum melt
Protection against aluminum bonding and welding
Improvement of sliding properties
- Release agent reduction
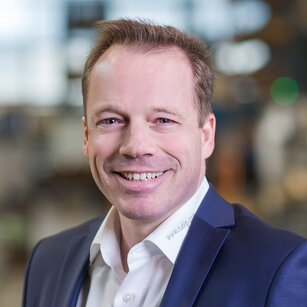
Maximum Protection for Your Components
PACVD delivers top-tier surface performance – and I’ll show you how to make the most of it. Let’s explore your options together!
DI David Unterberger
Head of Sales – Heat Treatment
Our coating line
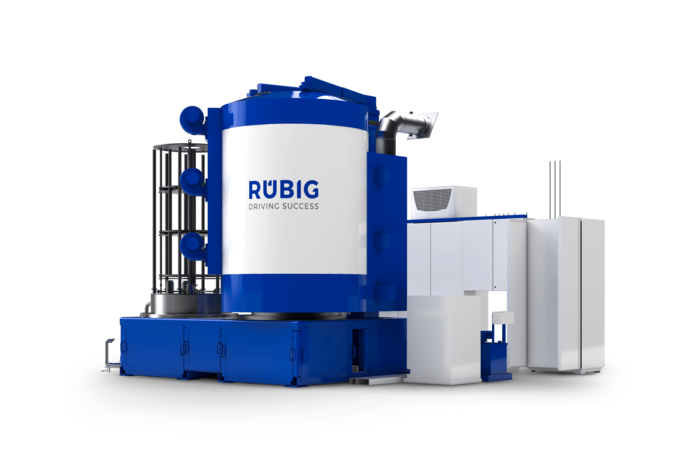
MICROPULS® Procoat
MICROPULS® Procoat coating systems enable the creation of premium hard coatings.