Maximum usable furnace space: Ø 1,500 mm/6,000 mm height
Maximum batch weight: 10.000 kg
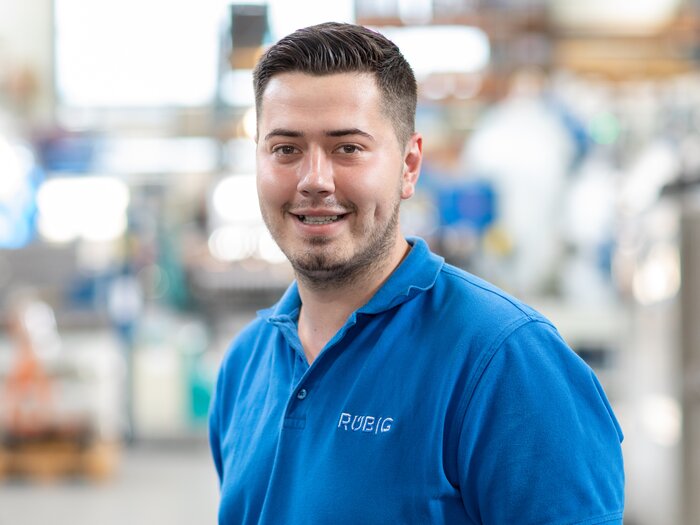
Under our brand name PLASNIT® we offer highly developed plasma nitriding heat treatments for a wide range of steel grades.
Our plasma nitriding system MICROPULS® Everest ensures plasma nitriding processes in premium quality with the RUBIG's MICROPULS® Technology.
PLASNIT® processes from RUBIG represent the technological top of nitriding technology and are constantly being further developed. The standard processes cover the recommended spectrum of nitriding hardness depth and compound layer thickness for all common, nitridable steels. In addition, we develop individual plasma nitriding processes to meet every requirement for nitriding hardness depth, compound layer thickness, corrosion protection and oxide layer thickness – for individual parts up to large series.
PLASNIT® stands for environmental friendliness, improved corrosion properties and the highest reproducibility.
Necessary information:
- Surface hardness
- Nitriding hardness depth
- Compound layer thickness/oxide layer thickness
- Definition of the area to be nitrided (as an indication on the construction drawing)
Our Plasma nitRIDING SYSTEM
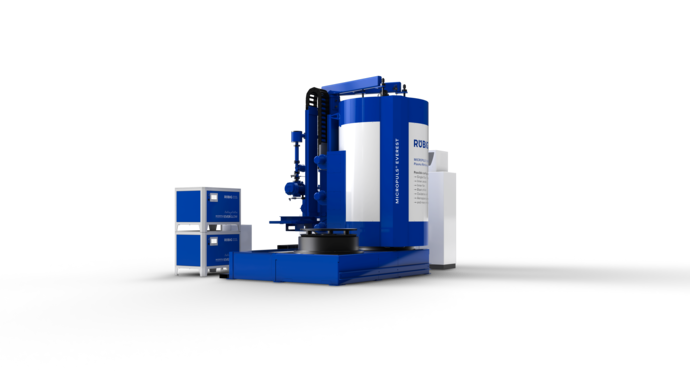
EVEREST
The plasma nitriding system MICROPULS® Everest offers our customers the cutting edge technology of nitriding. It is used in numerous industries, from automotive and contract heat treatment to aviation and wind energy.
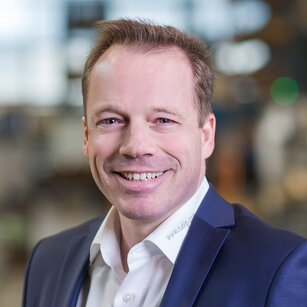
ANY QUESTIONS?
RUBIG Heat Treatment combines state-of-the-art technology and in-depth industry knowledge to optimise the finishing of your steel products.
DI David Unterberger
Head of Sales – Heat Treatment