Maximum usable furnace space: 1.200 x 900 x 900 mm (L x W x H)
Maximum batch weight: 2.500 kg
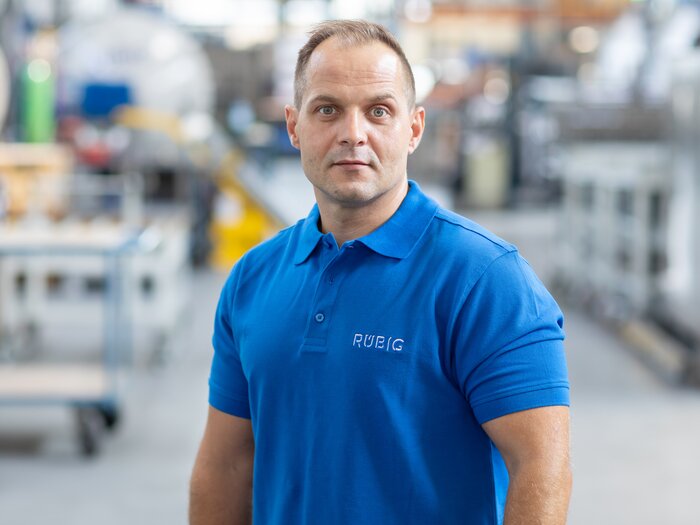
R.VAC+® stands for all vacuum hardening processes in RUBIG Heat Treatment.
Precise process control and unique quality standards enable uniform hardness, high toughness and an optimal structure of the components. Vacuum hardening is suitable for distortion-sensitive precision components, moldings and tools that have high requirements for a clean, bare surface.
R.VAC+® Process overview
Vacuum hardening
Vacuum hardening is the hardening process for distortion-sensitive precision components, molded parts and tools with high demands on a clean, bare surface. Quenching is carried out with a gas stream at an overpressure, which can be varied in order to adapt the cooling conditions to the component requirements.
Vacuum hardening in state-of-the-art vacuum furnaces
The workpieces remain metallically bright and show no changes on the surface (scaling, decarburizing), which results in a lower outlay for hard machining compared to other hardening processes (e.g. inert gas hardening). That is why expensive individual and serial tools as well as high-quality molds and components are heat-treated in the vacuum furnace.
Benefits:
Little delay
Metallic bare surfaces
Longer tool life
Precise documentation of the complicated process sequences
Absolutely reproducible treatment
Helivac®
HELIVAC® represents a special process of vacuum hardening, which is used with the highest requirements on the component properties.
The use of helium instead of nitrogen as a quenching medium results in the following benefits:
Advantages similar to vacuum hardening
Minimal delay
Maximum dimensional accuracy
LPC
Low underpressure carburizing (also low pressure carburizing/lpc) with subsequent gas quenching is a modern variant of case hardening. Compared to the classic gas carburizing with oil quenching, the benefits using vacuum technology in combination with gas quenching:
- Low delay
No edge oxidation
Also suitable for higher alloyed steels (no passivation)
Suitable materials:
All air-hardening case steels (e.g. M50NiL, 300M, 18CrNiMo7-6, 18CrNi8)
Also high-alloy steels (e.g. X38CrMoV5-1)
Benefits of low underpressure carburizing:
Optimum uniformity even with complicated component geometry and dense charging
Edge oxidation free surface
Clean and bare surface
Carburizing of high-alloy, passivating steels
Vacuum Brazing
Vacuum brazing or high-temperature brazing under vacuum is a thermal joining procedure in order to join materials/ components in a firm and bonded manner. With this method, complex geometries (e.g. complicated cooling channels) or several joints/seams can be connected in one process. Due to the high temperature in combination with a reduced pressure range (0.08 – 1 mbar), the material-dependent oxide layer is thermally broken up and thus replaces the use of flux.
Due to an optimal process control and appropriate soldering, the components can not only be firmly and materially connected to each other, but also hardened (vacuum hardening) at the same time. For this reason, we mainly use a copper base or nickel base solder. In order to create optimal solder joints, corresponding gaps and solder deposits must be taken into account already during the design.
Solution annealing and precipitation
Curing or aging (tempering) is always to be understood in combination with a previous solution heat treatment and quenching. As a result of this treatment, fine precipitations (coherent, partially coherent or incoherent) are formed in the basic matrix over time, depending on the material and temperature. These fine precipitations (phases) impede the movements of dislocations and thereby increase the strength.
The strength/hardness and the mechanical properties are determined by the aging temperature. Depending on the material (e.g. special stainless steels, maraging steels, titanium, aluminum alloys, bronze alloys), the aging temperature (tempering temperature) is in the range of 150°C – 500°C.
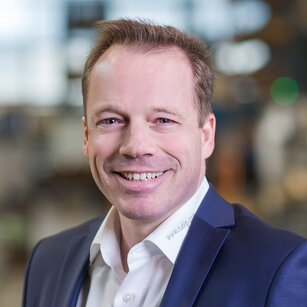
ANY QUESTIONS?
RUBIG Heat Treatment combines state-of-the-art technology and in-depth industry knowledge to optimise the finishing of your steel products.
DI David Unterberger
Head of Sales – Heat Treatment