The essential application properties of components and materials are often assessed on the basis of their mechanical properties. For metals, in addition to hardness testing, tensile strength testing is the most common mechanical and technological test method.
Testing the tensile strength of components
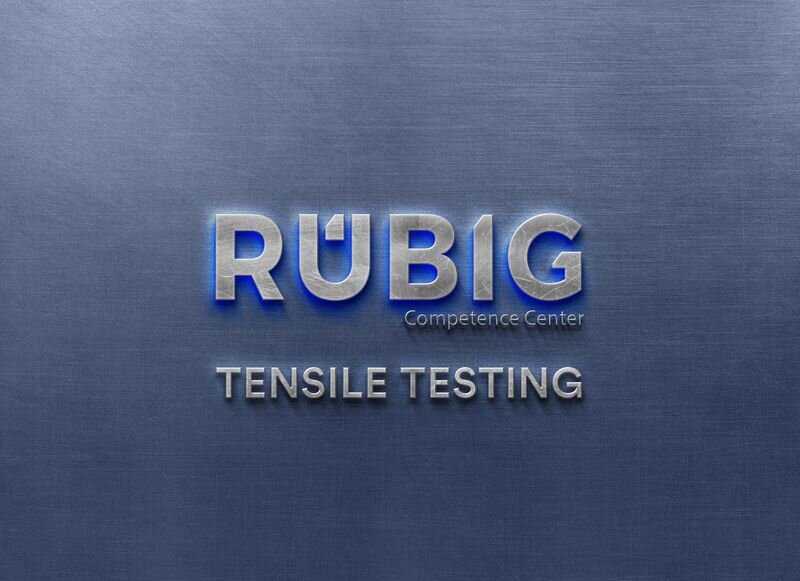
The tensile strength test provides a very good and comprehensive assessment of the material behavior under uniaxial quasi-static loading. The stress and strain coefficients, which are measured in the tensile test, are used in a variety of component calculations.
Even if it is possible to derive the tensile strength of metallic materials from the results of the hardness test under certain conditions, these derived values are only an estimate and are sometimes subject to considerable uncertainties. Reliable and accurate statements about the tensile strength are only possible by tensile strength testing. In addition to the tensile strength, other mechanical properties of the material can also be determined, such as the yield strength, the elongation at break and the constriction at break.