Malfunctions in a plant are unpleasant for every production operation. In order to return to normal as soon as possible, it is important to establish the cause of the disorder. The usual cause are leaks that often occur in the thermocouple feedthroughs, seals, valves or membranes.
Regular maintenance saves time and money
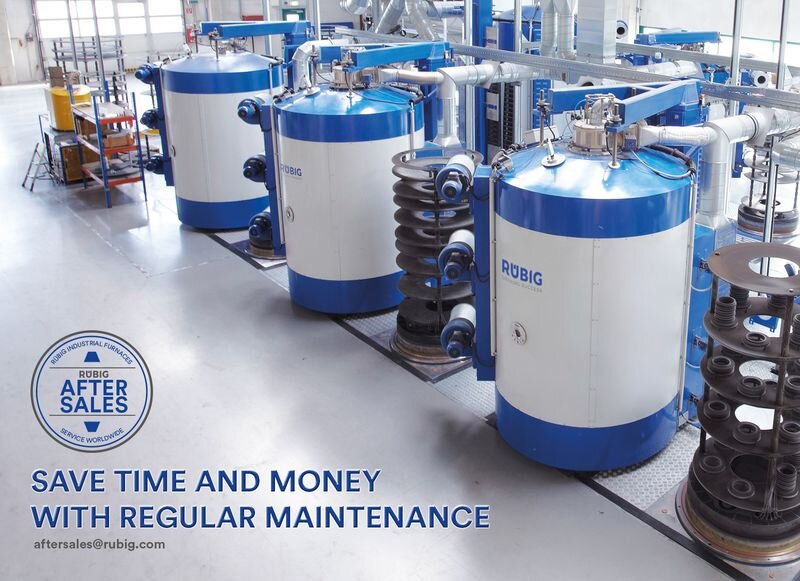
To determine the location of a leak, a leak test must be performed. In a first step, the system is evacuated down to 0.10 mbar. When 0.10 mbar is reached, the pressure regulating valve closes automatically and the pressure rise is measured (expressed in mbar*l/sec). A meaningful leak test should run for at least 2 hours. However, a poor leak rate does not necessarily indicate a leak. Impurities, lubricants on the batch, moisture in the system (for example, due to excessive oxidation), etc. could be other reasons. These impurities can evaporate gases into the vacuum, as a result of which the pressure in the system increases. A cleansing procedure often works wonders. Power outages, on the other hand, are less frequent causes of malfunctions. In the event of a power outage, the system immediately stops, and as soon as the power is back, the system resumes the process where it was interrupted. To summarize: regular maintenance of your system saves time, money and nerves. It reduces malfunctions to a minimum and can completely prevent system downtimes.
If you are interested in one of our maintenance packages, please contact our after Sales team.