Maximum oven usable space: Ø 1.500 mm / 2.400 mm height
Maximum batch weight: 7.500 kg
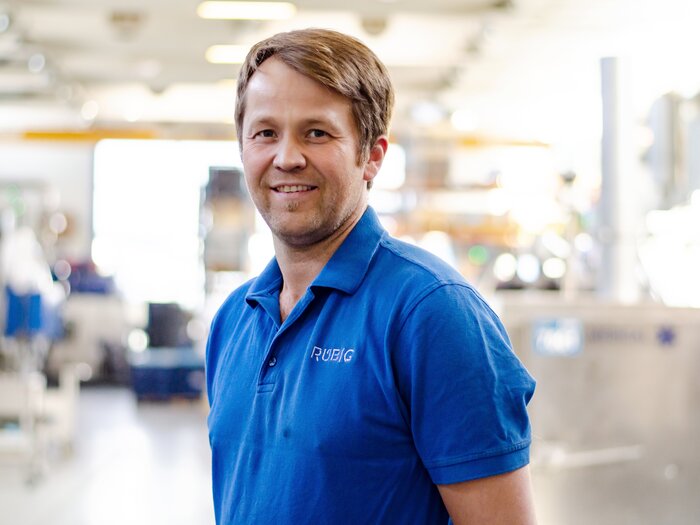
In gas nitriding, nitrogen is provided in the form of ammonia gas. The process takes place in bell and pit type furnaces at temperatures of 500°C to 600°C. Due to the chemical decomposition of the ammonia on the component, the nitrogen diffuses into the surface and forms a diffusion and bonding coating.
Process duration and temperature have a direct influence on the result. Hardness, nitration or hardening depth and coating thicknesses can be influenced by targeted process control. The additional enrichment of the surface with carbon is referred to as nitrocarburizing. A subsequent oxidation can be carried out during the cooling process or separately.
Low to medium alloyed steels are nitridable, but no passivated metallic surfaces. Component cleaning before treatment is of the greatest importance.
necessary information
- Material
- Surface hardness
- Nitriding hardness depth
- Compound layer thickness
- Oxide layer thickness
- Possible pre-treatments
- Should areas be protected (covered) before nitriding?
PROCEDURE
Short-term nitriding (nitrocarburizing)
Short-term nitriding + oxidizing
Normal nitriding
Long-term nitriding
Oxidize
TECHNICAL INFO
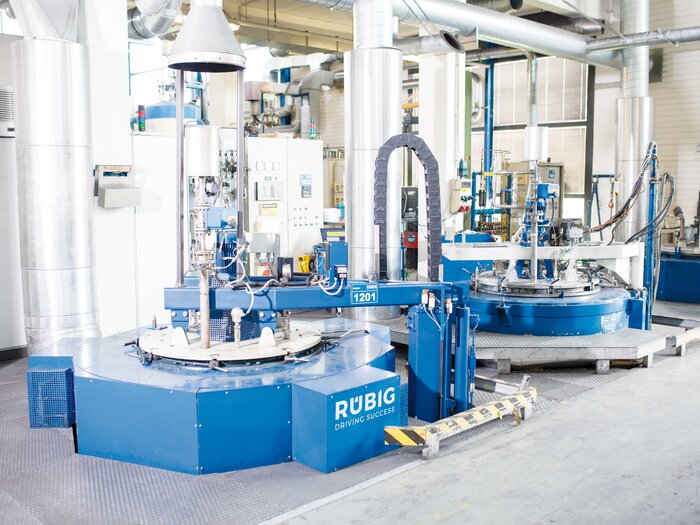
Suitable for:
Mechanical engineering, precision components, tool making, automotive industry, plastic injection molding technology, etc.
Material:
- Low to medium alloyed steels are nitridable
Possible surface preparation for an optimal surface condition:
- Free of greases, oils, processing agents or drawing and casting skins as well as sanding slips (barrel finishing)
Our gas nitriding system
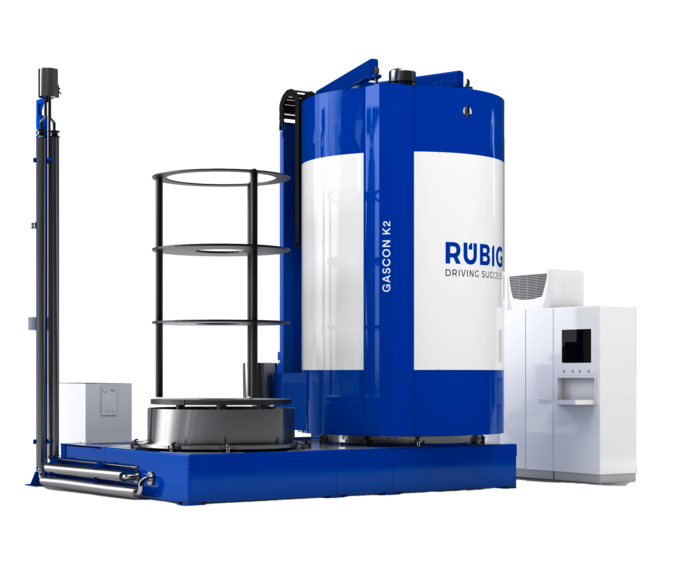
GASCON K2
RUBIG's gas nitriding systems are the result of decades of experience and further developments. RUBIG Industrial Furnaces' GASCON Technology stands for highly efficient and advanced gas nitriding.
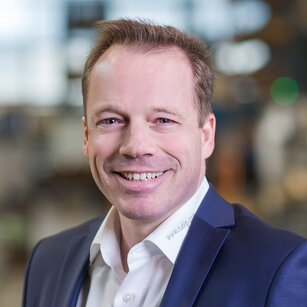
ANY QUESTIONS?
RUBIG Heat Treatment combines state-of-the-art technology and in-depth industry knowledge to optimise the finishing of your steel products.
DI David Unterberger
Head of Sales – Heat Treatment