PVD COATINGS
What is a PVD coating
and how does it work?
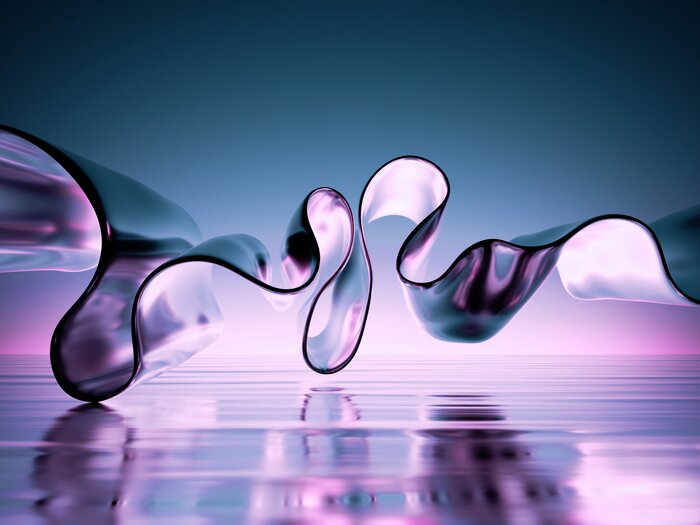
PVD coatings, based on Physical Vapor Deposition (PVD), are produced using a high-vacuum physical process. ) PVD is a process in which extremely thin yet highly durable hard material layers—or pure metallic films—are deposited onto metallic components. The primary goal is to significantly enhance the functionality of a workpiece—such as wear resistance, friction reduction, corrosion protection, and optical properties—without altering its dimensional accuracy.
PVD is employed wherever maximum performance, precision, and longevity are required, ranging from industrial components to decorative elements.
As a thin-film technology (up to approximately 5 µm), PVD allows for the coating of metals, glass, ceramics, plastics, and textiles. At RUBIG, these hard coatings are available in various colors.
We Coat Metals—and Much More
RUBIG's thin films are found on jewelry and fittings, in tool and mechanical engineering, automotive, transportation, and medical technology.
Layer Development Tailored to Your Requirements
Would you like to have PVD coatings perfectly matched to your needs? Contact us, and together we will find the ideal solution for you and your products! With our in-house PVD coating capabilities, we can also meet special requirements beyond standard coating systems.
The RUBIG Coating Center combines state-of-the-art equipment with cost-effective PVD coating processes to meet the highest standards.
How Does the PVD Process Work?
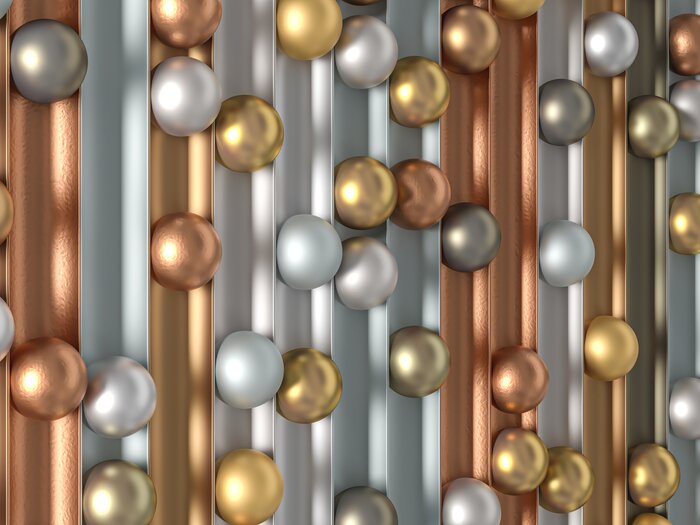
At RUBIG, Physical Vapor Deposition (PVD) stands for cutting-edge technology that takes the coating of components to a new level. In a high vacuum process, atoms and atomic clusters are deposited by a selected metallic target – such as titanium, chromium or copper. This advanced method includes techniques such as thermal evaporation, ion plating or the innovative magnetron sputtering, which we have perfected at RUBIG.
Our PVD process allows the production of extremely resistant hard coatings with a thickness of a few nm up to approximately 5 µm. By precisely activating the surface of the substrate material, we ensure excellent adhesion of the coating – a critical step for a long-lasting bond. The adaptability of this process is outstanding: not only a wide variety of metals, but also a variety of substrates can be used as coating materials – metals, ceramics, glass, plastics and even textiles can be refined.
A decisive advantage of RUBIG PVD technology is surface activation at low temperatures. This ensures that no distortion occurs even with heat-sensitive materials such as plastics.
With RUBIG's expertise in PVD coating technology, we are opening up new dimensions of surface finishing in order to meet the demanding requirements of our customers and to offer innovative solutions for a variety of applications.
Typical Applications of PVD Coatings
RUBIG PVD coatings are used in a wide range of industries and components - both for functional and decorative purposes:
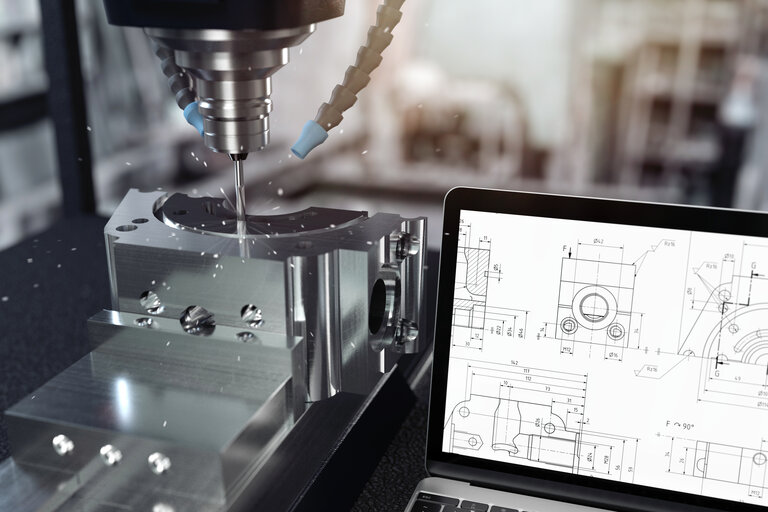
Tool and Mold Making
- Cutting tools: mills, drills, taps
- Forming tools: punches, dies
- Aluminum die casting and plastics processing
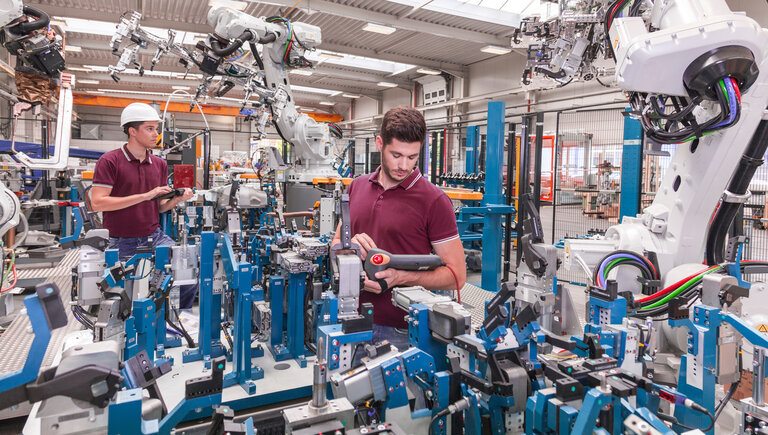
Mechanical &
Plant Engineering
- Bearings, piston rings, valves, seals
- Components with micro-movements or tight tolerances
- Alternative to hard chrome in food processing technology
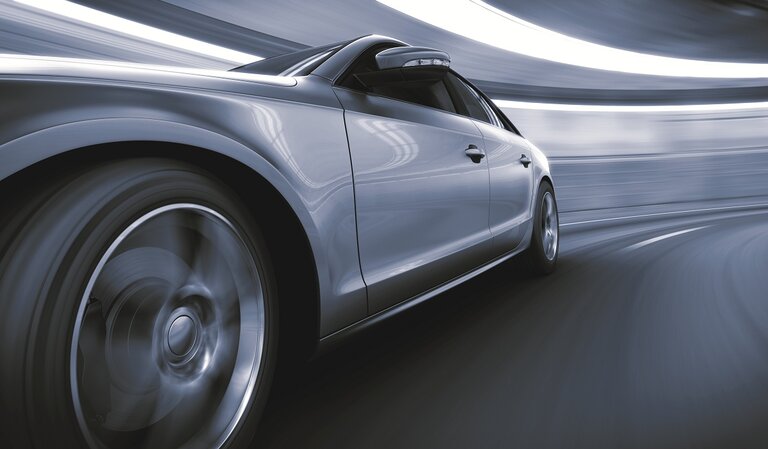
Transportation & Automotive
- Piston pins, valve discs, injection systems
- Engine components subject to friction
- Parts exposed to corrosion or high temperatures
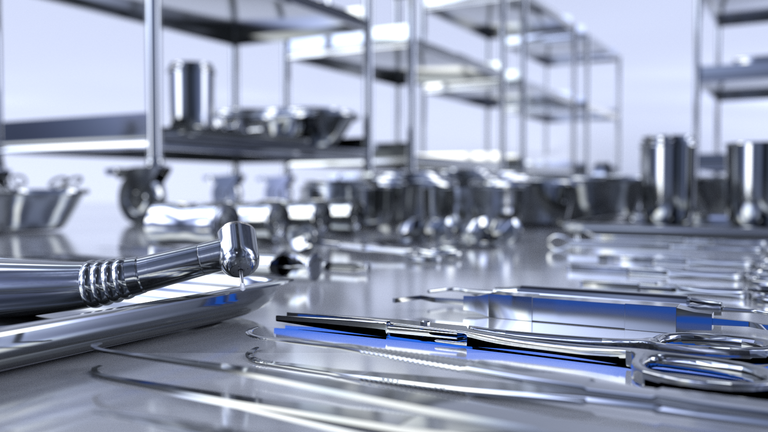
Medical Technology & Hygiene Applications
- Biocompatible coating systems
- Antibacterial and antiviral variants (e.g., Cu/CuO)
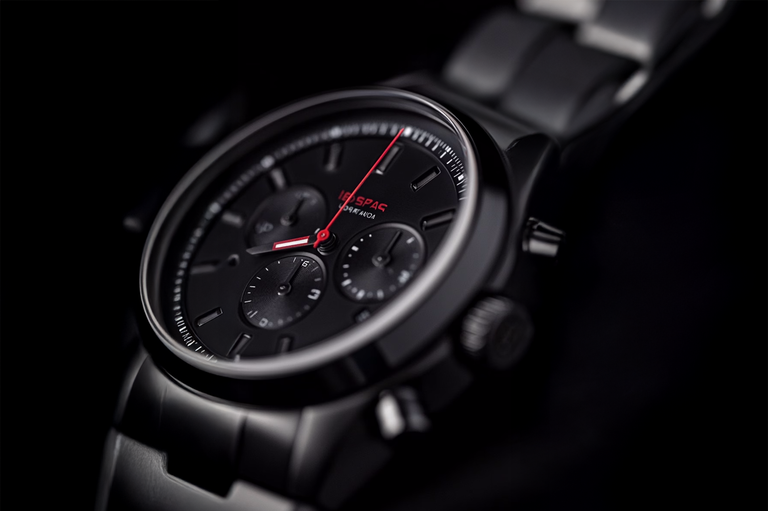
Design & Lifestyle
- Watches, Jewelry, Fittings
- Door and furniture hardware
- Decorative colors such as gold, anthracite, bronze, and white gold
Overview of Our Coating Systems
RUBIG offers a broad portfolio of standard and custom coatings:
Coating System | Color | Typical Properties |
---|---|---|
TiN | Gold | Universally applicable, high hardness |
TiCN | Steel blue to violet | Ideal for forming, stamping, and thread cutting of stainless steel |
CrN / CrCN | Metallic silver / grey | Excellent sliding and corrosion resistance, suitable for plastics processing |
ZrN / ZrCN | White gold to gold / copper to bronze | Decorative, aluminum/titanium machining, forming, medical technology |
MoS₂-basiert | Anthracite grey | Ideal for plastics processing, non-stick, minimizes friction in vacuum |
Cu / CuO | Copper / black | Electrically conductive, antibacterial |
Cr-CrO | Silver to rainbow | Ideal for plastics processing, reduced adhesion, good demolding properties (PC, PMMA) |
PVD Systems –
Technology & Sustainability at RUBIG
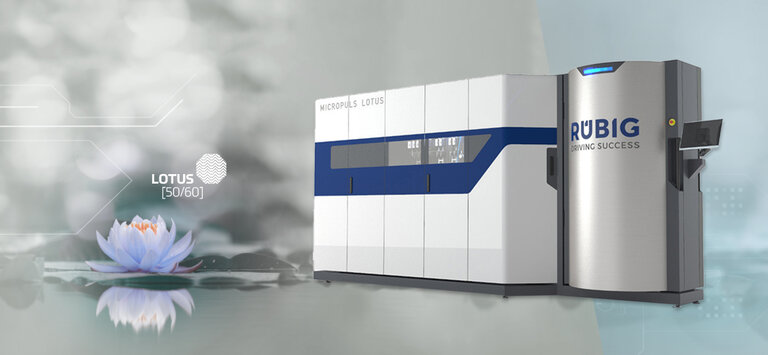
RUBIG relies on state-of-the-art equipment, such as the in-house MICROPULS® Lotus PVD system, to achieve the highest coating quality in a cost-effective and reproducible manner.
At RUBIG, PVD coatings provide a precise, environmentally friendly, and economical solution for highly stressed components in industry and engineering.
- Coating of single parts, small batches, and industrial series components
- Environmentally friendly process: no toxic chemicals, reduced resource consumption
- Reproducible quality through comprehensive coating analysis
FAQ:
Frequently Asked Questions
about PVD Coatings
Not sure which solution is right for you?
PVD & PACVD
Compare now
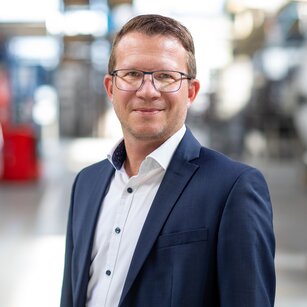
Questions about the ideal coating solution?
PVD is your perfect coating - and my specialty.
Let's connect!
DI Dr. Christian Dipolt MBA
Managing Director RUBIG Technology
A key advantage is surface activation at low temperatures.
This ensures that even heat-sensitive materials such as plastics do not experience any distortion.