Overview procedures
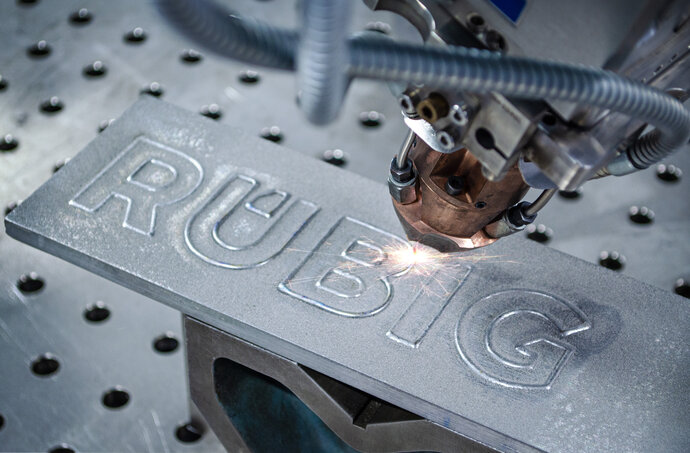
Laser deposition welding with laser metal deposition
The technology is ideally suited for wear and corrosion protection coatings, functional surfaces, additive elements and the repair of worn parts (e.g. jaw linings). It impresses with a large selection of powders (steel, aluminum, titanium, nickel, cobalt, etc.) in grain sizes up to 150 µm and a low mixing with the base material.
Areas of application:
- Tool and mold making
- Cutting and punching tools
- Forging dies
- Soil treatment parts
- Blades and chopping knives
Application examples:
- Wear protection coatings (e.g. SiC in aluminum matrix)
- Anti-corrosion coatings
- Functional surfaces
- Additive elements
- Repair of worn parts (e.g. jaw lining)
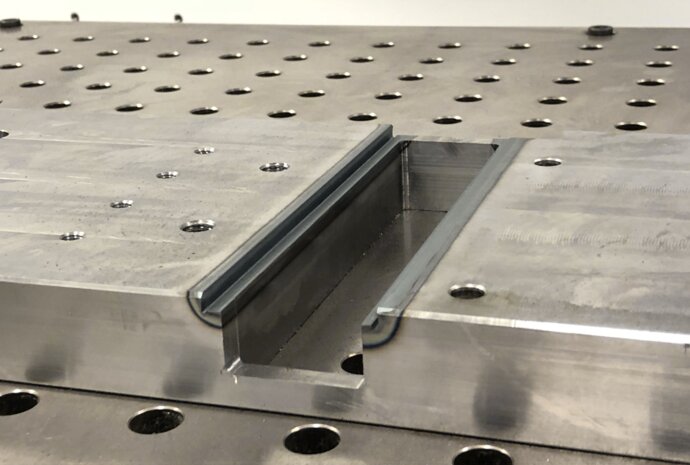
Laser hardening
For all curable steels and cast irons, RUBIG offers local, selective hardening of surfaces with hardening depths up to 1.5 mm (larger depths upon request) and track widths up to max. 30 mm. The technology is low in distortion, requires little to no rework and is very flexible thanks to CNC control. An integrated pyrometer measures the temperature and regulates the power so as not to damage sharp-edged transitions.
Application examples:
- Machine components
- Cutting and punching tools
- Thermoforming tools
- Forming tools
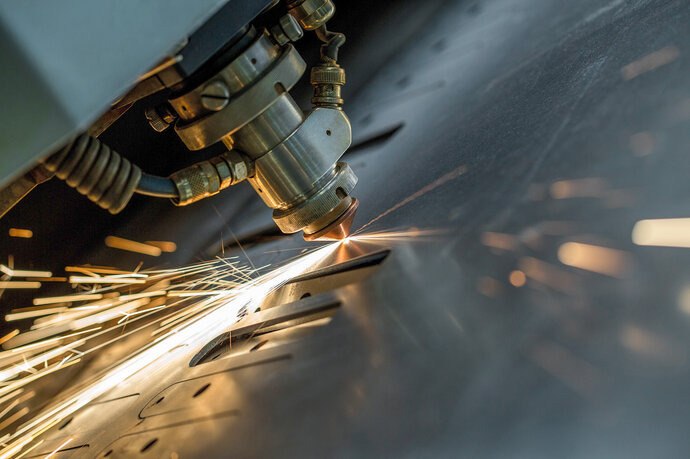
3D Laser Cutting
Our system cuts sheets of steel, corrosion-resistant steels, aluminum, etc. up to a thickness of 5 mm.
Application examples:
- Deep-drawn components (hole, final cut)
- Tubes / Shaped tubes
- Sheet metal welding assemblies
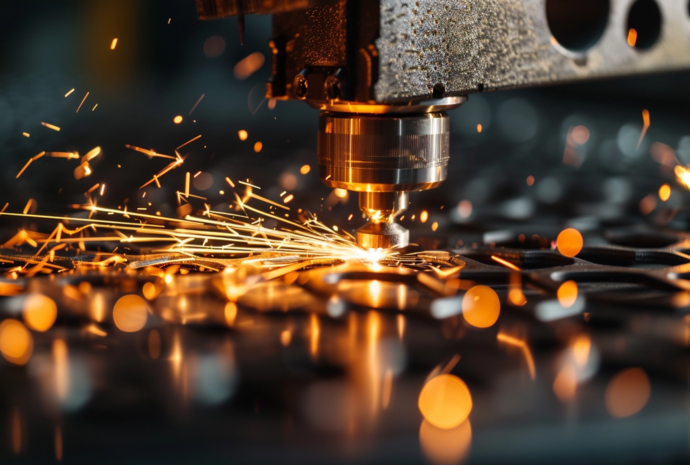
Laser welding
Due to the targeted introduction of heat, there is hardly any delay with this technology. It is suitable for steel, corrosion-resistant steels, aluminum, etc. (welding gas argon / helium, spot diameter approx. 450 µm, technical zero gap required).
Application examples:
- Machine components
- Sheet metal assemblies
- and many more
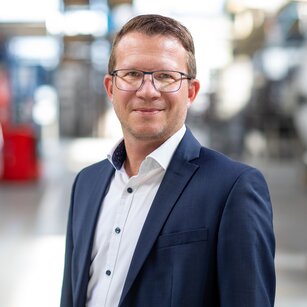
High-End Laser Technology
Rely on RÜBIG’s laser processes for precise and efficient treatment of your components.
Contact me for a personal consultation!
DI Dr. Christian Dipolt MBA
Managing Director RUBIG Technology