In recent years, wind energy has become one of the most important renewable energy sources worldwide. In order to ensure their reliable and efficient long-term operation, the components of wind turbines must withstand the stresses to which they are exposed during operation.
RUBIG Know-how in wind turbines
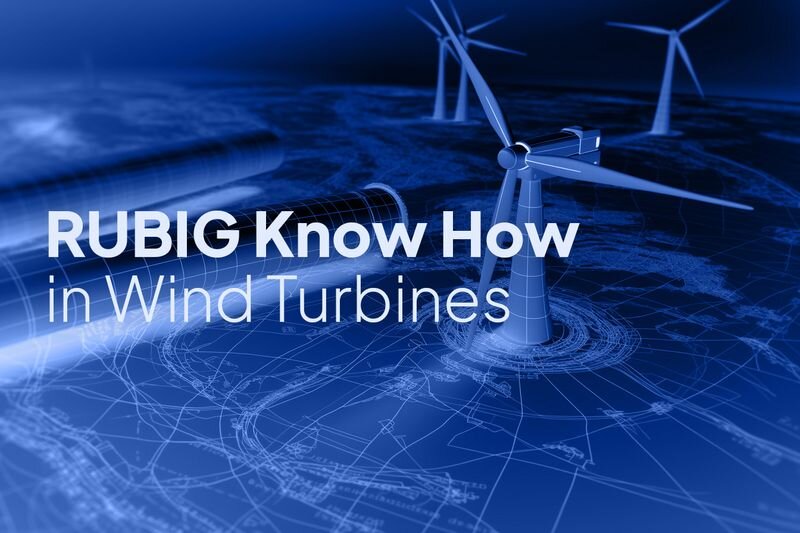
A key component in wind turbines are plain bearings, which ensure low-friction rotation of the rotor blades. These bearings are exposed to high mechanical forces, vibrations and adverse environmental conditions. In order to increase their service life and improve their performance, high-quality surface treatments such as nitriding and coating are applied.
We give plain bearings the perfect properties
A well-known customer of RUBIG was faced with the challenge of designing plain bearings for wind turbines with a long service life and high efficiency. They contacted the RUBIG R&D team to find the right solution. After clarifying the feasibility, the team recommended a DLC coating to solve the problem. With the "Diamond Like Carbon" coating, the nitriding and coating processes are combined in one operation.
Before the components were coated, the RUBIG experts carried out some tests to ensure that the customer requirements were fulfilled 100 percent. For this purpose, a sample cookie was examined in the nanoindenter and tribometer and then subjected to a scratch test.
Nanoindenter: How hard is the coating?
In this test method, the hardness is determined. Even the thinnest coatings can be examined and low test loads of 1 mN are possible.
Scratch test: How good is the adhesion and the wear behavior?
This test is used to determine the adhesion and wear behavior of coatings. With a continuously increasing test load, the sample table is moved and a "scratch" is created. This is then examined under a microscope.
Tribometer: How good is the friction and wear behavior?
The tribological properties of coatings are determined using the tribometer. In particular, the friction and wear behavior are analyzed.
The customer also carried out tests with the coating. In this way, weak points, performance limits and potential for improvement could be identified.
From sample cookies to serial production
Subsequently, test parts were coated and further validation by the customer followed before the actual plain bearings were coated. After a further characterization, the Real Life test was carried out. This test took about a year before an assessment was executed. After all tests were completed positively, RUBIG was given the green light to transfer the coating to series production.
In addition to plain bearings, there are other components such as gears, valve train components or piston pins that must have special tribological properties.
Do you also have corresponding components that you would like to improve technically? Contact GE Volker Strobl MSc from our research and development team. Together we will find the perfect solution for a subsequent series production.
Put your trust in RUBIG, your expert for heat and surface treatments.