True to the motto "One seamlessly integrates into the other", RUBIG is expanding its competence in the automation of nitriding plants
AUTOMATION SHAPES INDUSTRY
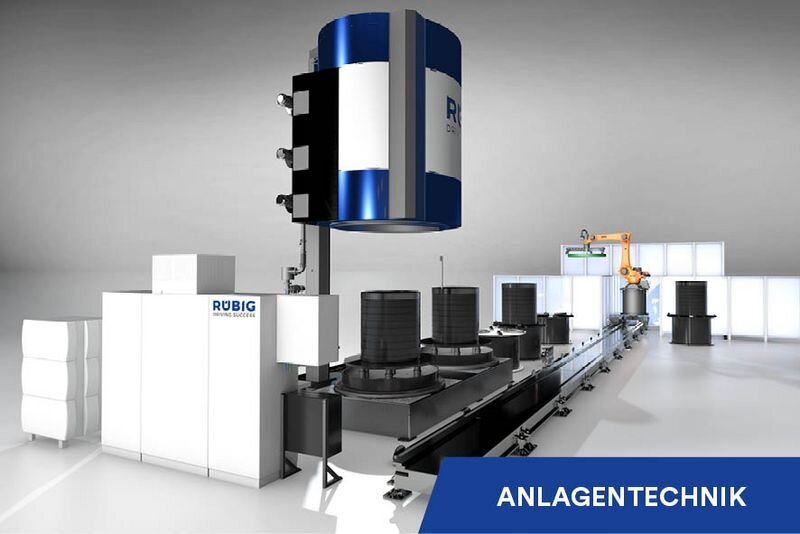
RUBIG Industrial Furnaces designs and produces tailor-made metal heat treatment plants in detail. Both the plasma nitriding technology "MICROPULS®" developed by RUBIG, as well as the gas nitriding process "GASCON" confirm RUBIG as a worldwide reference in this segment. In order to be able to produce in a future-proof manner, companies cannot avoid the automation of heat treatment plants. A complete system solution, combined with perfectly coordinated processes, reduces manual processes to a minimum. In-depth knowledge of service providers in machining and processing is just as much an elementary factor as experience and economic solutions. Investments must meet the requirements of today, but at the same time be fit for the industrial future. In other words: Industry 4.0. An even smaller, but quickly rising market in the already large automation spectrum are "complete solutions" in heat treatment.
Automotive Case Study
More and more automobile manufacturers are confronted with the problem of applying high-quality wear protection to transmission parts and at the same time coping with short cycle times and high quantities. RUBIG's solution is an autonomous system in which only the charging plate has to be loaded manually. The rest of the work is done by a specially produced manipulator. This gripper picks up the fully loaded batching plates and places them precisely on one of the nitriding systems. Alternatively, if necessary, the plates are placed on a buffer table. A lifting turntable ensures an ergonomic mode of operation during manual loading of the batching plate. The system can be adjusted steplessly through pneumatic operation, which makes filling much easier. Modern, powerful PLC programs allow the beginner to obtain suitable values for recipe creation via proven standard parameters. The experienced user, on the other hand, is offered an instrument to perform all changes to the control parameters himself. The data recording, in which ready-made and user-defined trends can be viewed, facilitates quality assurance. All settings and process data are logged in real time – one hundred percent traceability is thus guaranteed. Constant technological advances in the field of plasma nitriding technology, which is used in a wide variety of industries from automotive and contract heat treatment to aviation and wind energy, have brought the company to the top in the international competition.