Maximum Profitability:
Plasma Nitriding System
Pays Off in 1.5 Years
From outsourcing to in-house:
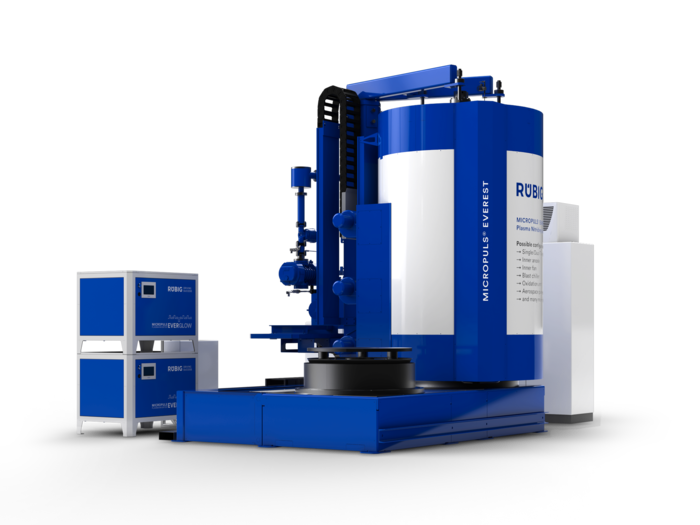
A Central European forging company demonstrates how internalizing the nitriding process can become a strategic success story. With the MICROPULS® Everest plasma nitriding system from RUBIG, the decision to handle nitriding in-house proved spot-on: the investment paid for itself in just 1.5 years.
The application: plasma nitriding of forging dies with a batch weight of up to 7.5 tons.
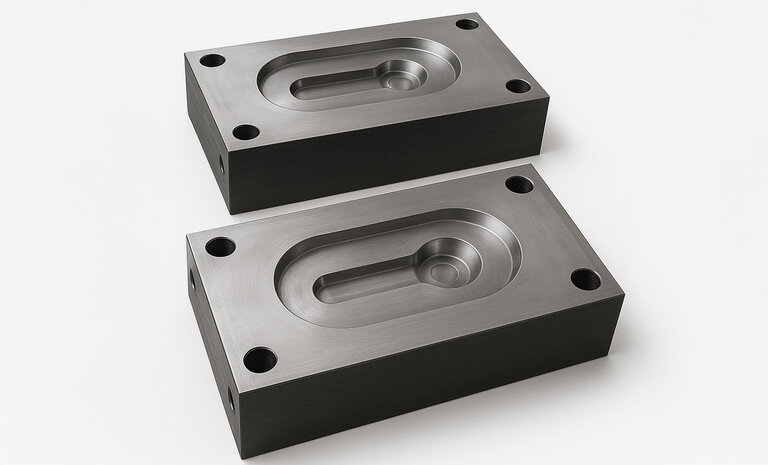
FORGING DIES –NITRIDED FOR PERFORMANCE
Plasma nitriding delivers significant surface hardening, resulting in longer tool life and a notable reduction in unit costs.
Read the technical article
A Strategic Advantage
In times of rising costs and global uncertainty, more and more companies are shifting toward in-house processes. For forging operations, this means less dependence on external service providers, greater delivery reliability, and faster response times.
From a certain number of parts or batch sizes, production costs per component can be reduced significantly.
More Flexibility –
Shorter Lead Times
Traditional outsourcing often involves several days of delay between shipping, processing, and return. With an in-house system, this logistical effort is eliminated. The result: faster production, closer coordination with quality assurance, and the ability to react quickly to customer requests or process deviations.
Significant Savings
with Full Control
The economic benefit is clear: no transport costs, no packaging, no waiting times, and no additional service fees. In-house plasma nitriding costs only a fraction of outsourced treatment – while giving you greater control over process and quality.
Getting Started with In-House Nitriding
Bringing the nitriding process in-house is easier than many companies expect – and often overestimated. Plasma nitriding in particular is ideally suited for internal implementation:
- No hazardous substances: No toxic chemicals, open flames, or harmful vapors involved
- Minimal structural modifications: No need to retrofit production halls
- No complex exhaust systems: No afterburners or separate exhaust lines required
- Low space requirements: Thanks to minimal gas consumption, large gas tanks are unnecessary
- Simple operation: Once process parameters are defined for the specific material and requirements, even less experienced personnel can safely operate the system
4 reasons: In-house plasma nitriding
In-house plasma nitriding
is a strategic advantage
Economically, technically, and organizationally. The successful implementation at the forging plant proves:
The MICROPULS® Everest enables maximum profitability in the shortest possible time.
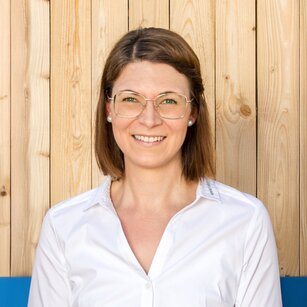
In-house Nitriding
Pays Off
Less external dependency, shorter lead times, and significantly lower unit costs make all the difference.
Learn more now and secure your competitive advantage!
Sabine Kreuzmayr MA
Sales Manager - Industrial Furnaces